Method for Surface Coating of Explosive Particles
A surface coating and explosive technology, applied in explosives, explosive processing equipment, offensive equipment, etc., can solve the problems of unavoidable particles, low film thickness, low paraffin melting point, etc., and achieve complete coating and ultra-thin coating. , Solve the effect of particle aggregation and strong high temperature resistance
- Summary
- Abstract
- Description
- Claims
- Application Information
AI Technical Summary
Problems solved by technology
Method used
Image
Examples
Embodiment 1
[0027] In this embodiment, the paraffin wax is coated on the surface of the explosive particle HMX, and the coating thickness is
[0028]15g of paraffin wax was placed in the heating furnace of the vacuum deposition device, 2g of HMX explosive particles (average particle size 200 μm) was placed in the rotatable powder deposition device, and the deposition chamber door was closed. After evacuating to a pressure of less than 30mbar, maintain the vacuum. Turn on the heating device of the heating furnace to 300°C, and at the same time turn on the rotation button of the rotatable powder deposition device to make it rotate and drive the HMX explosive particles inside to rotate and roll together. The paraffin gas generated after heating the paraffin enters the rotary device through the reserved channel of the powder rotary deposition device, contacts with the HMX explosive particles and deposits on the surface of the explosive particles. When deposited to the online quartz thickne...
Embodiment 2
[0032] In this embodiment, the paraffin wax is coated on the surface of the explosive particle HMX, and the coating thickness is
[0033] Others of this embodiment are the same as those of Embodiment 1, except that the deposition thickness is Recording this sample coating degree is 100%, friction sensitivity is 20%, impact sensitivity is 0%, electrostatic spark sensitivity (E 50 ) is 1.88J.
Embodiment 3
[0035] In this embodiment, the paraffin wax is coated on the surface of the explosive particle HMX, and the coating thickness is
[0036] Others of this embodiment are the same as those of Embodiment 1, except that the deposition thickness is Recording this sample coverage is 100%, friction sensitivity is 10%, impact sensitivity is 0%, electrostatic spark sensitivity (E 50 ) is 2.55J.
PUM
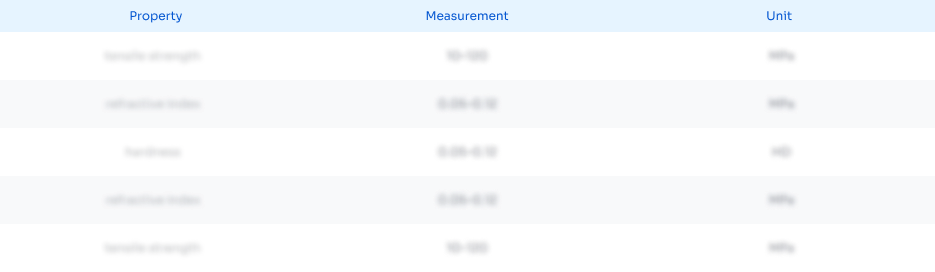
Abstract
Description
Claims
Application Information

- R&D
- Intellectual Property
- Life Sciences
- Materials
- Tech Scout
- Unparalleled Data Quality
- Higher Quality Content
- 60% Fewer Hallucinations
Browse by: Latest US Patents, China's latest patents, Technical Efficacy Thesaurus, Application Domain, Technology Topic, Popular Technical Reports.
© 2025 PatSnap. All rights reserved.Legal|Privacy policy|Modern Slavery Act Transparency Statement|Sitemap|About US| Contact US: help@patsnap.com