A rubber grinding machine for rubber rollers
A grinding machine and rubber roller technology, which is applied in the direction of cutting tools for lathes, turning equipment, metal processing machinery parts, etc., can solve the problem of destroying the dynamic balance of the steel core, the rigidity of the steel core, the destruction of the dynamic balance of the metal rod, and dust pollution in the operating place, etc. problems, to improve the processing technology, reduce the waste of energy and raw materials, and facilitate the effect of brushing and drying
- Summary
- Abstract
- Description
- Claims
- Application Information
AI Technical Summary
Problems solved by technology
Method used
Image
Examples
Embodiment Construction
[0031] The present invention will be further described below in conjunction with the accompanying drawings and embodiments.
[0032] like figure 1 and figure 2 As shown, a special rubber grinding machine for rubber rollers includes a bedside 1 and a bed 2 connected in sequence, the bedside 1 is provided with a headstock 3, the bedside 2 is provided with a tailstock 4, and a workpiece 5 Fixed between the headstock 3 and the tailstock 4, the bed 2 below the workpiece 5 is provided with a large carriage 6, the large carriage 6 is provided with a slider 12 and a gear 13, and the bed 2 is provided with The first linear guide rail 14 and the rack 15, the slide block 12 cooperates with the first linear guide rail 14, the gear 13 cooperates with the rack 15, and the large carriage 6 is provided with In the front middle carriage 7 and the rear middle carriage 8, a knife rest 9 is installed on the front middle carriage 7, and an abrasive belt grinder 10 is installed on the rear middl...
PUM
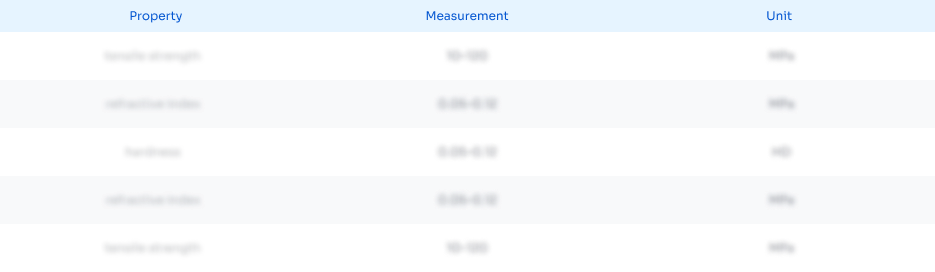
Abstract
Description
Claims
Application Information

- Generate Ideas
- Intellectual Property
- Life Sciences
- Materials
- Tech Scout
- Unparalleled Data Quality
- Higher Quality Content
- 60% Fewer Hallucinations
Browse by: Latest US Patents, China's latest patents, Technical Efficacy Thesaurus, Application Domain, Technology Topic, Popular Technical Reports.
© 2025 PatSnap. All rights reserved.Legal|Privacy policy|Modern Slavery Act Transparency Statement|Sitemap|About US| Contact US: help@patsnap.com