Method for brazing ZrB2-SiC composite ceramic material by using Pd-Co-Ni brazing filler metals
A pd-co-ni, composite ceramic technology, applied in the direction of welding/cutting media/materials, welding media, welding equipment, etc., can solve the problems of reducing the performance of the base material, to reduce the strength of the base material, effectively connect, weaken reciprocal effect
- Summary
- Abstract
- Description
- Claims
- Application Information
AI Technical Summary
Problems solved by technology
Method used
Image
Examples
specific Embodiment approach 1
[0015] Specific embodiment one: In this embodiment, a kind of use Pd-Co-Ni solder brazing ZrB 2 -The method of SiC composite ceramic material is carried out by following steps: one, the preparation of Pd-Co-Ni brazing filler metal: be 1 by mass ratio: (2~3): the ratio of (1~2) takes Pd powder body, Co powder and Ni powder, mixed to obtain mixed solder powder, and then add binder to the mixed solder powder to obtain a mixed paste solder, wherein the binder consists of 1.wt% hydroxyl Ethyl cellulose and 99.wt% distilled water are configured;
[0016] 2. Assembling the sample: Use 280#, 800# and 1000# metallographic sandpaper to separate two pieces of ZrB 2 - The surface to be welded of the SiC ceramic base material is polished step by step, and the polished ZrB 2 -SiC ceramic base material is placed in 99% acetone solution by mass percentage, ultrasonically cleaned for 10min to 20min, then cleaned with absolute ethanol, and then dried, and the paste solder is coated on two cle...
specific Embodiment approach 2
[0019] Embodiment 2: This embodiment differs from Embodiment 1 in that the purity of the Pd powder, Co powder and Ni powder described in step 1 is not less than 99%. Others are the same as the first embodiment.
specific Embodiment approach 3
[0020] Embodiment 3: The difference between this embodiment and Embodiment 1 or 2 is that the Pd powder, Co powder and Ni powder are weighed in the ratio of atomic weight 1:2.36:1.18 in Step 1. Others are the same as those in Embodiment 1 or 2.
PUM
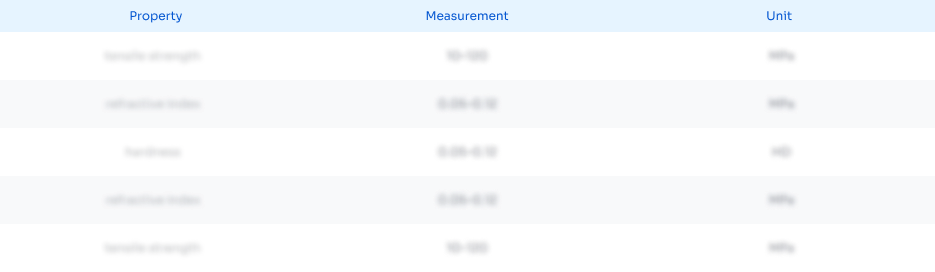
Abstract
Description
Claims
Application Information

- R&D
- Intellectual Property
- Life Sciences
- Materials
- Tech Scout
- Unparalleled Data Quality
- Higher Quality Content
- 60% Fewer Hallucinations
Browse by: Latest US Patents, China's latest patents, Technical Efficacy Thesaurus, Application Domain, Technology Topic, Popular Technical Reports.
© 2025 PatSnap. All rights reserved.Legal|Privacy policy|Modern Slavery Act Transparency Statement|Sitemap|About US| Contact US: help@patsnap.com