Alloy powder and method for welding galvanized steel sheet and az91d magnesium alloy based on laser synchronous powder feeding
A technology of laser synchronous powder feeding and galvanized steel sheet, applied in laser welding equipment, welding equipment, metal processing equipment and other directions, can solve the problems of easy deterioration of welded joint performance, difficult control of the melting degree of magnesium alloy, low melting point of magnesium alloy, etc. Achieve the effect of ideal engineering practical significance, flexible formula and high welding efficiency
- Summary
- Abstract
- Description
- Claims
- Application Information
AI Technical Summary
Problems solved by technology
Method used
Image
Examples
Embodiment 1
[0017] The clamping of the materials to be welded is as follows: figure 1 As shown, it is a composite process of laser welding + synchronous powder feeding. The AZD91 magnesium alloy 1 is a flat plate with a thickness of 3 mm, and the galvanized steel sheet 2 is a flat plate with a thickness of 3 mm. The high entropy alloy powder 200 mesh AlMg 0.1 After the CuZn medium is evenly mixed with a ball mill (600 rpm, ball milling for 30 minutes), it is sent to the overlapping area of the workpiece to be welded by the powder feeder through the channel 4, and the welding seam 5 is formed under the irradiation of the laser beam 3 and the action of the inert gas 6 . Set the four main welding parameters as follows: laser power P=3kW, welding speed v=2m / min, powder feeding amount q=20g / min, lap gap 0.08mm.
Embodiment 2
[0019] The clamping of the materials to be welded is as follows: figure 1 As shown, it is a composite process of laser welding + synchronous powder feeding. The AZD91 magnesium alloy 1 is a flat plate with a thickness of 3 mm, and the galvanized steel plate 2 is a flat plate with a thickness of 3 mm. High entropy alloy powder 250 mesh AlMg 0.2 After the CuZn medium is evenly mixed with a ball mill (600 rpm, ball milling for 30 minutes), it is sent to the overlapping area of the workpiece to be welded by the powder feeder through the channel 4, and the welding seam 5 is formed under the irradiation of the laser beam 3 and the action of the inert gas 6 . Set the four main welding parameters as follows: laser power P=4kW, welding speed v=2.5m / min, powder feeding amount q=25g / min, lap gap 0.09mm.
Embodiment 3
[0021] The clamping of the materials to be welded is as follows: figure 1 As shown, it is a composite process of laser welding + synchronous powder feeding. The AZD91 magnesium alloy 1 is a flat plate with a thickness of 3 mm, and the galvanized steel plate 2 is a flat plate with a thickness of 3 mm. High entropy alloy powder 300 mesh AlMg 0.3 After the CuZn medium is evenly mixed with a ball mill (600 rpm, ball milling for 30 minutes), it is sent to the overlapping area of the workpiece to be welded by the powder feeder through the channel 4, and the welding seam 5 is formed under the irradiation of the laser beam 3 and the action of the inert gas 6 . The four main welding parameters are set as follows: laser power P=5kW, welding speed v=3m / min, powder feeding amount q=30g / min, lap gap 0.1mm.
PUM
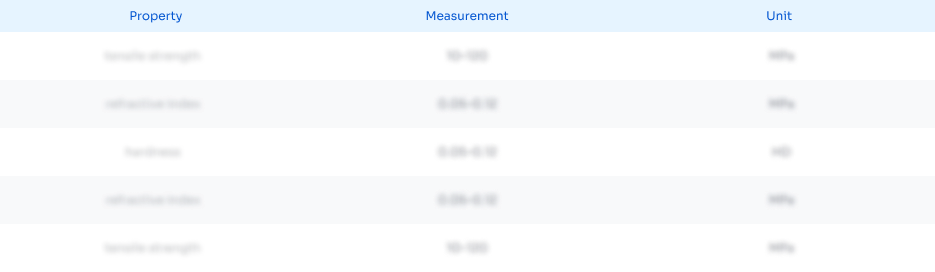
Abstract
Description
Claims
Application Information

- R&D
- Intellectual Property
- Life Sciences
- Materials
- Tech Scout
- Unparalleled Data Quality
- Higher Quality Content
- 60% Fewer Hallucinations
Browse by: Latest US Patents, China's latest patents, Technical Efficacy Thesaurus, Application Domain, Technology Topic, Popular Technical Reports.
© 2025 PatSnap. All rights reserved.Legal|Privacy policy|Modern Slavery Act Transparency Statement|Sitemap|About US| Contact US: help@patsnap.com