Method for building lubricating oil film model after thermal mechanical coupling deformation of hydrostatic thrust bearing
A technology of thermomechanical coupling and static pressure thrust, which is applied in special data processing applications, instruments, electrical digital data processing, etc., can solve the problems of workpiece efficiency and accuracy, and achieve the improvement of machine tool speed, safe operation avoidance, and avoidance of lubrication failure. Effect
- Summary
- Abstract
- Description
- Claims
- Application Information
AI Technical Summary
Problems solved by technology
Method used
Image
Examples
specific Embodiment approach 1
[0016] Specific Embodiment 1: In this embodiment, a method for establishing a lubricating oil film model after thermal coupling deformation of a hydrostatic thrust bearing is implemented in the following steps:
[0017] Step A. Based on the dimensional structure of the test machine tool and the given initial oil film thickness, use 3D modeling software to build models of the workbench, base, fan-shaped oil chamber and initial oil film, assemble the workbench, base and oil chamber, and export to zhuangpei .x_t and youmo.x_t files (where the workbench and base are 1 / 12 models);
[0018] Step B. Use GAMBITZ software to mesh the initial oil film to obtain a high-quality mesh, specify the boundary conditions of the fluid domain and output the youmo.fluent5 / 6mesh file, and import the youmo.fluent5 / 6mesh file into FLUENT to input or select the oil film inlet temperature T in Initial value, initial value of oil film fixed wall surface temperature, oil film inlet flow rate Q, outlet p...
specific Embodiment approach 2
[0024] Embodiment 2: This embodiment differs from Embodiment 1 in that: in step A, the workbench and the base are analyzed using a 1 / 12 model. Other steps and parameters are the same as those in Embodiment 1.
specific Embodiment approach 3
[0025] Specific embodiment three: the difference between this embodiment and specific embodiment one or two is that step C establishes a work flow chart in the ANSYSWOERKBECH software, and performs thermal coupling calculation and analysis on the static pressure thrust bearing as follows:
[0026] Step C1, import the fluid analysis results, add the FLUENT module, import the youmo.cas file in step B into FLUENT and re-calculate iteratively;
[0027] Step C2, import the assembly model, add the Geometry geometric module, and import the zhuangpei.x_t file in step A;
[0028] Step C3, thermal analysis, insert the Steady-State Thermal module, and set the material properties of the workbench, base and oil chamber. Since only thermal analysis and linear structural analysis are required, it is only necessary to fill in the corresponding density, Yang modulus, Poisson's ratio and thermal conductivity; the results of fluid analysis are imported into thermal analysis, and the temperature ...
PUM
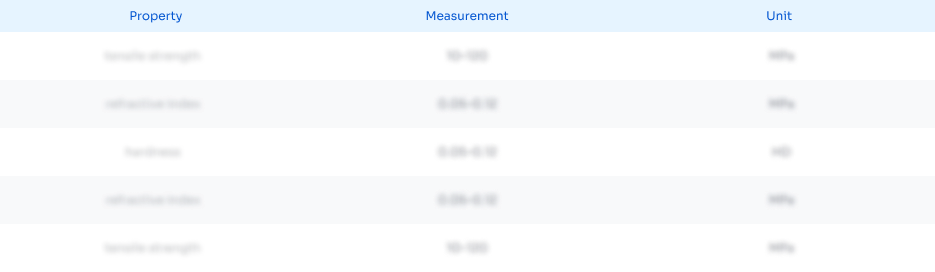
Abstract
Description
Claims
Application Information

- R&D
- Intellectual Property
- Life Sciences
- Materials
- Tech Scout
- Unparalleled Data Quality
- Higher Quality Content
- 60% Fewer Hallucinations
Browse by: Latest US Patents, China's latest patents, Technical Efficacy Thesaurus, Application Domain, Technology Topic, Popular Technical Reports.
© 2025 PatSnap. All rights reserved.Legal|Privacy policy|Modern Slavery Act Transparency Statement|Sitemap|About US| Contact US: help@patsnap.com