Numerical simulation method for temperature and thickness relation of static thrust bearing gap oil film based on film thickness variation
A technology of hydrostatic thrust and bearing clearance, applied in the field of fluid mechanics simulation, can solve problems such as overestimation of equipment safety, failure to consider oil film thickness, unfavorable safe operation of equipment, etc., and achieve the effect of increasing rotational speed and shortening design cycle.
- Summary
- Abstract
- Description
- Claims
- Application Information
AI Technical Summary
Problems solved by technology
Method used
Image
Examples
specific Embodiment approach 1
[0038] Specific implementation mode one: as Figure 1-7 As shown, the specific process of the numerical simulation method for the relationship between the oil film temperature and the thickness of the hydrostatic thrust bearing gap based on the variable film thickness described in this embodiment is as follows:
[0039] Step A, establish the parent model of the oil film in the gap of the hydrostatic thrust bearing: give the initial value of the thickness of the oil film, and use the modeling function of Unigraphics NX software to establish the parent model of the oil film in the gap of the hydrostatic thrust bearing;
[0040] Step B, pre-processing: In ANSYS ICEM CFD software, perform pre-processing on the hydrostatic thrust bearing clearance oil film parent model generated in the above step A, mesh the fluid domain constructed by the above hydrostatic thrust bearing clearance oil film parent model, and Specify fluid domain boundary conditions;
[0041] Step C, CFX oil film f...
specific Embodiment approach 2
[0060] Specific implementation mode two: as Figure 1-7 , 8 to 11, the numerical simulation method for the relationship between the oil film temperature and the thickness of the hydrostatic thrust bearing gap based on the variable film thickness described in this embodiment, in step A, use the modeling function of the Unigraphics NX environment to establish the hydrostatic thrust The specific process of bearing clearance oil film parent model is as follows:
[0061] Step A1, using the Unigraphics NX environment to perform reverse modeling of the oil film in the gap of the hydrostatic thrust bearing;
[0062] Step A2, parameterize all the dimensions involved in the reverse modeling, and obtain the corresponding expressions;
[0063] Step A3, establishing an oil film model modeling human-computer interaction interface;
[0064] Step A4, establish two functional sub-modules: the sub-module of obtaining model parameters in real time and displaying them immediately, and the sub-m...
specific Embodiment approach 3
[0067] Specific implementation mode three: as Figure 1-7 , Figure 8-11 , Figures 12 to 14 As shown, in the numerical simulation method for the relationship between the oil film temperature and the thickness of the hydrostatic bearing based on the variable film thickness described in this embodiment, in step B, the ANSYS ICEMCFD software is run for pre-processing, and the specific steps are as follows:
[0068] Step B1, automatically import the hydrostatic thrust bearing clearance oil film parent model established in step 1 in ANSYS ICEM CFD software;
[0069] Step B2, establishing standardized auxiliary points and auxiliary lines, so that all auxiliary points are attached to the curve or surface; all auxiliary lines are attached to the curved surface;
[0070] Step B3. Reconstruction of missing surfaces on the oil film model: After the oil film model is imported into the ANSYS ICEM CFD environment, there may be missing or distorted surfaces at the outlet of the oil film, an...
PUM
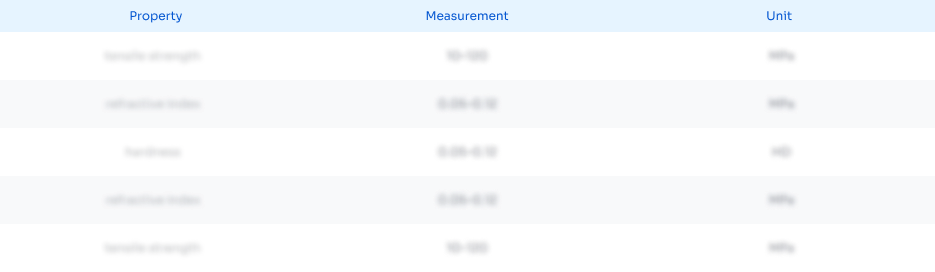
Abstract
Description
Claims
Application Information

- R&D
- Intellectual Property
- Life Sciences
- Materials
- Tech Scout
- Unparalleled Data Quality
- Higher Quality Content
- 60% Fewer Hallucinations
Browse by: Latest US Patents, China's latest patents, Technical Efficacy Thesaurus, Application Domain, Technology Topic, Popular Technical Reports.
© 2025 PatSnap. All rights reserved.Legal|Privacy policy|Modern Slavery Act Transparency Statement|Sitemap|About US| Contact US: help@patsnap.com