Riveting process of pieces of sheet metal
A riveting and process technology, applied in the field of multi-piece metal riveting process, can solve the problems of falling off, poor electrical conductivity of the whole part, discount of parts performance, etc., and achieve the effect of simple operation
- Summary
- Abstract
- Description
- Claims
- Application Information
AI Technical Summary
Problems solved by technology
Method used
Image
Examples
Embodiment Construction
[0018] The following will clearly and completely describe the technical solutions in the embodiments of the present invention with reference to the drawings in the embodiments of the present invention.
[0019] according to figure 2 and 3 , the multi-piece metal riveting process provided by the present invention includes:
[0020] Punch one of the metal sheets;
[0021] The rest of the metal sheets are made into convex hulls, and the convex hulls 22 correspond to the positions of the holes 21;
[0022] Lay the convex-hulled metal sheets in sequence, with the convex-hull 22 facing upwards and the direction of the burrs punching in the same direction;
[0023] Place the hole 21 of the punched metal sheet corresponding to the convex hull 22 of the convex metal sheet, and be located on the uppermost layer of the metal sheet;
[0024] Position the stacked metal sheets in the mold;
[0025] The activation die stamps and forms stacked sheets of metal to form a complete assembly...
PUM
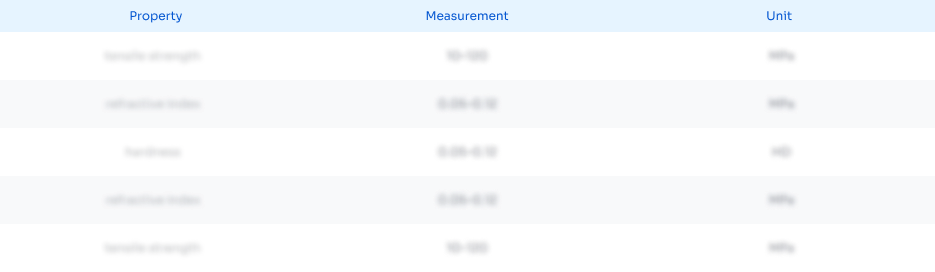
Abstract
Description
Claims
Application Information

- R&D
- Intellectual Property
- Life Sciences
- Materials
- Tech Scout
- Unparalleled Data Quality
- Higher Quality Content
- 60% Fewer Hallucinations
Browse by: Latest US Patents, China's latest patents, Technical Efficacy Thesaurus, Application Domain, Technology Topic, Popular Technical Reports.
© 2025 PatSnap. All rights reserved.Legal|Privacy policy|Modern Slavery Act Transparency Statement|Sitemap|About US| Contact US: help@patsnap.com