Method for producing beta-methylnaphthalene by using coal tar washing oil for continuously distilling
A technology of methylnaphthalene and coal tar, applied in the directions of azeotropic distillation, distillation purification/separation, fractionation, etc., can solve the problems of low industrial β-methylnaphthalene yield, low degree of automation, low labor productivity, etc. Effects of control and regulation, high level of automation, high labor productivity
- Summary
- Abstract
- Description
- Claims
- Application Information
AI Technical Summary
Problems solved by technology
Method used
Image
Examples
Embodiment Construction
[0021] The present invention will be described in further detail below through embodiments in conjunction with the accompanying drawings.
[0022] See figure 2 , a method for producing β-methylnaphthalene by continuous distillation of coal tar washing oil. The method adopts three-tower continuous distillation, and after rectification treatment in the last rectification tower, the amount of β-methylnaphthalene is cut out from the top of the tower or the side line For industrial β-methylnaphthalene products with ≥95% and indole ≤0.2%, the α-methylnaphthalene component or industrial α-methylnaphthalene is cut from the bottom of the tower; the azeotropic solvent is separated from the methylnaphthalene fraction and reused; Specific steps are as follows:
[0023] 1) Coal tar washing oil raw material (containing β-methylnaphthalene, about 80% of α-methylnaphthalene) rich in α-methylnaphthalene and β-methylnaphthalene fraction after pretreatment, and entrainer (B Glycol, diethylene...
PUM
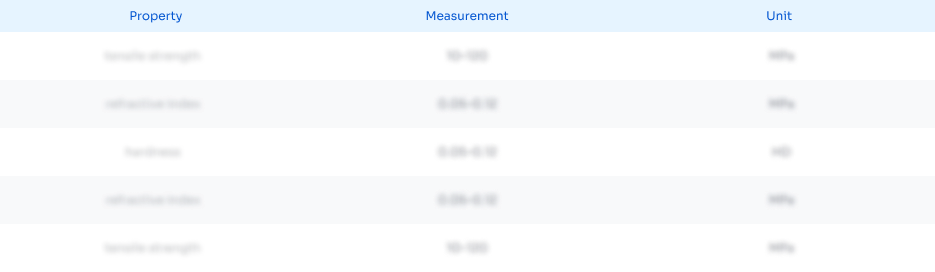
Abstract
Description
Claims
Application Information

- R&D
- Intellectual Property
- Life Sciences
- Materials
- Tech Scout
- Unparalleled Data Quality
- Higher Quality Content
- 60% Fewer Hallucinations
Browse by: Latest US Patents, China's latest patents, Technical Efficacy Thesaurus, Application Domain, Technology Topic, Popular Technical Reports.
© 2025 PatSnap. All rights reserved.Legal|Privacy policy|Modern Slavery Act Transparency Statement|Sitemap|About US| Contact US: help@patsnap.com