Composite aluminum-base brazing wire for continuously brazing aluminum alloy and method for manufacturing composite aluminum-base brazing wire
A composite aluminum and aluminum alloy technology, applied in welding equipment, metal processing equipment, welding media, etc., can solve the problems of insufficient brazing process, melting and scrapping, and uncommon application, so as to achieve stable and good joint performance and improve durability Corrosion, excellent overall performance
Inactive Publication Date: 2013-07-17
GUILIN QINGTONG NON FERROUS METAL ARTS & CRAFTS MATERIAL DEV CO LTD
View PDF6 Cites 16 Cited by
- Summary
- Abstract
- Description
- Claims
- Application Information
AI Technical Summary
Problems solved by technology
Because there is a layer of dense oxide film on the surface of the base metal, the aluminum solder cannot be wetted, and the brazing process cannot take place; at the same time, the presence of the solder on the surface of the base metal hinders the flux from covering, infiltrating, and stripping the base metal. In the process of removing the oxide film, the removal of the oxide film is not complete, leaving a large amount of residual oxide film, which makes the brazing process insufficient, reduces the brazing rate of the brazed joint, causes the joint to have low strength, is easy to desolder and break, and has poor reliability; at the same time Pores, cracks, water leakage, water seepage, air leakage and other brazing defects are prone to occur, and many repairing hours are required, and the appearance quality of the brazing seam is poor; also because the brazing temperature of Al-Si(12) flux-cored aluminum brazing wire is high, it is close to the base metal melting point, it is easy to cause over-burning of the base metal, coarse grains, reduced strength, or even melting and scrapping
At present, flux-cored aluminum brazing wire is mainly used for continuous brazing of industrial pure and a small number of aluminum alloy structural parts with light load, and it is not widely used in automobile manufacturing industry.
Method used
the structure of the environmentally friendly knitted fabric provided by the present invention; figure 2 Flow chart of the yarn wrapping machine for environmentally friendly knitted fabrics and storage devices; image 3 Is the parameter map of the yarn covering machine
View moreImage
Smart Image Click on the blue labels to locate them in the text.
Smart ImageViewing Examples
Examples
Experimental program
Comparison scheme
Effect test
Embodiment 1
Embodiment 2
Embodiment 3
the structure of the environmentally friendly knitted fabric provided by the present invention; figure 2 Flow chart of the yarn wrapping machine for environmentally friendly knitted fabrics and storage devices; image 3 Is the parameter map of the yarn covering machine
Login to View More PUM
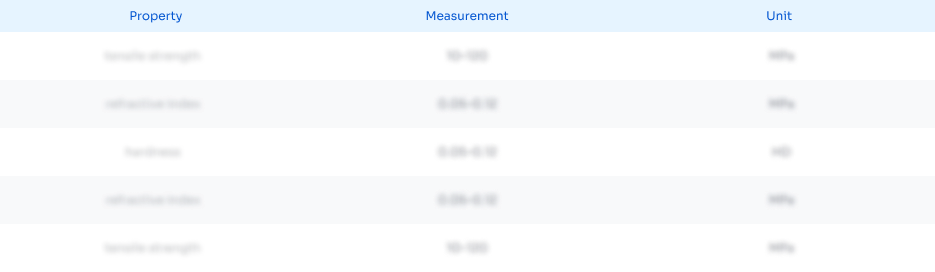
Abstract
The invention discloses a composite aluminum-base brazing wire for continuously brazing aluminum alloy and a method for manufacturing the composite aluminum-base brazing wire. The aluminum-base brazing wire comprises a section of aluminum-base brazing filler metal, non-corrosive brazing fluxes for aluminum and silicon powder coating layers; the section of the aluminum-base brazing filler metal is provided with grooves, the non-corrosive brazing fluxes for the aluminum are composited in the grooves of the section, and the silicon powder coating layers are coated on surfaces of the brazing fluxes; and the section side of the section of the brazing filler metal can be provided with one groove or two grooves or three grooves. The method includes smelting and casting the brazing filler metal of the brazing wire during manufacture and squeezing a blank which is a rod; manufacturing the section of the brazing filler metal of the brazing wire by means of rolling and squeezing; compositing the section of the brazing filler metal with the non-corrosive brazing fluxes for the aluminum; and coating the silicon powder coating layers on the surfaces of the composite brazing fluxes. The composite aluminum-base brazing wire and the method have the advantages that the local composite aluminum-base brazing wire for continuously brazing the aluminum alloy is suitable for intelligent brazing equipment provided with a laser brazing system, so that the intelligent brazing equipment can be used for continuously brazing various medium and large aluminum alloy structural parts with over-burning temperatures higher than 580 DEG C, the quality of brazing seams is stable, and the efficiency is high.
Description
technical field [0001] The invention belongs to the technical field of aluminum-based brazing material, and in particular relates to a composite aluminum-based brazing wire applied to continuous brazing of aluminum alloys and a preparation method thereof. Background technique [0002] In recent years, the wide application of high-strength aluminum alloys in aviation, aerospace, communications, automobiles, rail transit vehicles, electronics, home appliances and other industries has promoted the development of welding technology and promoted the structural adjustment of my country's welding consumables industry. It has become a trend for continuous brazing local composite aluminum-based brazing wire to replace other similar types of aluminum welding wire. [0003] At present, there are two methods for aluminum alloy welding: one is fusion welding, that is, the solid aluminum welding wire (filler) and the base metal are melted and solidified at the same time to form a weld, and...
Claims
the structure of the environmentally friendly knitted fabric provided by the present invention; figure 2 Flow chart of the yarn wrapping machine for environmentally friendly knitted fabrics and storage devices; image 3 Is the parameter map of the yarn covering machine
Login to View More Application Information
Patent Timeline

Patent Type & Authority Applications(China)
IPC IPC(8): B23K35/14B23K35/24B23K35/363B23K35/365B23K35/40
Inventor 阳家盛
Owner GUILIN QINGTONG NON FERROUS METAL ARTS & CRAFTS MATERIAL DEV CO LTD
Features
- R&D
- Intellectual Property
- Life Sciences
- Materials
- Tech Scout
Why Patsnap Eureka
- Unparalleled Data Quality
- Higher Quality Content
- 60% Fewer Hallucinations
Social media
Patsnap Eureka Blog
Learn More Browse by: Latest US Patents, China's latest patents, Technical Efficacy Thesaurus, Application Domain, Technology Topic, Popular Technical Reports.
© 2025 PatSnap. All rights reserved.Legal|Privacy policy|Modern Slavery Act Transparency Statement|Sitemap|About US| Contact US: help@patsnap.com