Stabilizing process for Er-containing Al-Mg cold rolled sheet with high Mg content
An aluminum alloy and stabilization technology, applied in the field of stabilization technology, can solve the problems of poor resistance to intergranular corrosion, achieve the effects of refining grains, maintaining stable mechanical properties, and improving intergranular corrosion resistance
- Summary
- Abstract
- Description
- Claims
- Application Information
AI Technical Summary
Problems solved by technology
Method used
Image
Examples
Embodiment 1
[0043] Step 1), step 2) are the same as those in comparative example 2, step 3), the difference is that the alloy cold-rolled sheet is annealed at 220°C for different times. The change curve of weight loss per unit area with annealing time is as follows: Figure 8 shown.
Embodiment 2
[0045] Step 1), step 2) are the same as those in comparative example 2, step 3), the difference is that the alloy cold-rolled sheet is annealed at 230°C for different times. The change curve of weight loss per unit area with annealing time is as follows: Figure 9 shown.
[0046] Depend on Figure 2 to Figure 9 It can be seen that after the alloy is annealed at 100°C to 200°C, as the annealing time prolongs, the weight loss of the alloy gradually increases, and its intergranular corrosion resistance decreases. The elongation continued to increase, but it was found by metallographic observation that intergranular corrosion also occurred. Compared with other temperatures, the weight loss curve of the alloy at 220°C to 230°C presents a completely different trend, and the weight loss of the alloy does not change with the prolongation of the annealing time, and has remained at about 2mg / cm 2 , has been in the intergranular corrosion resistance zone, showing excellent intergranul...
Embodiment 3
[0049] Step 1), step 2) are the same as Comparative Example 1.
[0050] 3) Anneal the cold-rolled sheet of Er-containing medium-high Mg aluminum alloy at 220°C for different times, and measure the microhardness of the cold-rolled sheet at 220°C with the annealing time, as shown in Figure 11 shown. Depend on Figure 11 It can be seen that the hardness of the alloy decreases greatly after annealing at 220 °C for 1 hour, from 141HV to 119.8HV, and decreases slowly with the further extension of annealing time, and finally tends to be stable. In order to ensure that the mechanical properties of cold deformed alloys after stabilization annealing at 220 °C remain at a high level, the stabilization annealing time needs to be determined. It can be seen from Comparative Example 1 that the hardness value corresponding to the starting recrystallization temperature of the alloy cold-rolled sheet is 113.2HV, and the hardness value of the alloy in the 220°C / 12-hour annealed state correspo...
PUM
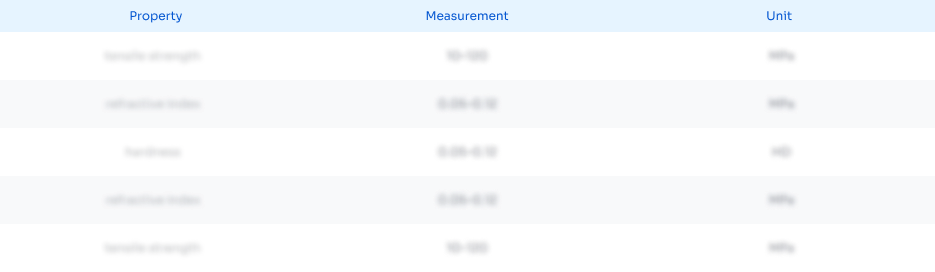
Abstract
Description
Claims
Application Information

- R&D Engineer
- R&D Manager
- IP Professional
- Industry Leading Data Capabilities
- Powerful AI technology
- Patent DNA Extraction
Browse by: Latest US Patents, China's latest patents, Technical Efficacy Thesaurus, Application Domain, Technology Topic, Popular Technical Reports.
© 2024 PatSnap. All rights reserved.Legal|Privacy policy|Modern Slavery Act Transparency Statement|Sitemap|About US| Contact US: help@patsnap.com