Polyolefin/styrene based resin composition and preparation method thereof
A technology of styrene-based resin and styrene copolymer, which is applied in the field of polyolefin/styrene-based resin composition and its preparation, can solve problems such as poor compatibility, complex synthesis process, and poor material performance, and achieve excellent mechanical properties , excellent strength, good toughness and chemical resistance
- Summary
- Abstract
- Description
- Claims
- Application Information
AI Technical Summary
Problems solved by technology
Method used
Image
Examples
Embodiment 1
[0026] (1) Weigh 100 parts of polypropylene copolymer, 800 parts of acrylonitrile-butadiene-styrene copolymer, 50 parts of compatibilizer PP-G, 40 parts of toughening agent butadiene copolymer 181H, processing aid 5 parts of EBS, 2 parts of main antioxidant auxiliary agent 1010 and 3 parts of auxiliary antioxidant 168.
[0027] (2) put the polypropylene copolymer, acrylonitrile-butadiene-styrene copolymer, compatibilizer, toughening agent, anti-oxidation aid, processing aid weighed in the first step together into a rotating speed of 150 Mix thoroughly in a high-speed mixer at rpm for 3 minutes.
[0028] (3) Use a precise metering and conveying device to send the mixed material in the second step into the twin-screw extruder, and through the shearing action of the screw, fully mix, wherein the aspect ratio of the twin-screw extruder is 40 , the screw speed is 300 rpm, the working temperature range of the twin-screw extruder is 180°C at the feeding port, 195°C at the metering s...
Embodiment 2
[0031] (1) Weigh 200 parts of polypropylene copolymer, 650 parts of acrylonitrile-butadiene-styrene copolymer, 50 parts of compatibilizer PP-G, 90 parts of toughening agent, 5 parts of processing aid EBS, main antibiotic 2 parts of oxidation aid and 3 parts of auxiliary antioxidant.
[0032] (2) The polypropylene copolymer, acrylonitrile-butadiene-styrene copolymer, compatibilizer, toughening agent, anti-oxidation aid and processing aid taken in the first step are put into together and the rotating speed is 120 Mix thoroughly in a high-speed mixer at rpm for 3 minutes.
[0033] (3) Use a precise metering and conveying device to send the mixed material in the second step into the twin-screw extruder, and through the shearing action of the screw, fully mix, wherein the aspect ratio of the twin-screw extruder is 40 , the screw speed is 300 rpm, the working temperature range of the twin-screw extruder is 175°C at the feeding port, 190°C at the metering section, 195°C at the melti...
Embodiment 3
[0036] (1) Weigh 400 parts of polypropylene copolymer, 400 parts of acrylonitrile-butadiene-styrene copolymer, 50 parts of compatibilizer PP-G, 50 parts of compatibilizer ABS-G, toughening agent butadiene 90 parts of quasi-copolymer 181H, 5 parts of processing aid EBS, 2 parts of main antioxidant auxiliary agent and 3 parts of auxiliary antioxidant.
[0037] (2) put the polypropylene copolymer, acrylonitrile-butadiene-styrene copolymer, compatibilizer, toughening agent, anti-oxidation aid, processing aid taken in the first step together into a rotating speed of 100 Mix thoroughly in a high-speed mixer at rpm for 3 minutes.
[0038] (3) Use a precise metering and conveying device to send the mixed material in the second step into the twin-screw extruder, and through the shearing action of the screw, fully mix, wherein the aspect ratio of the twin-screw extruder is 40 , the screw speed is 300 rpm, the working temperature range of the twin-screw extruder is 180°C at the feeding ...
PUM
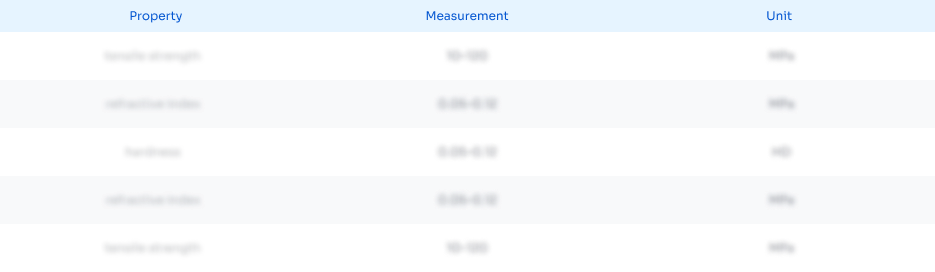
Abstract
Description
Claims
Application Information

- Generate Ideas
- Intellectual Property
- Life Sciences
- Materials
- Tech Scout
- Unparalleled Data Quality
- Higher Quality Content
- 60% Fewer Hallucinations
Browse by: Latest US Patents, China's latest patents, Technical Efficacy Thesaurus, Application Domain, Technology Topic, Popular Technical Reports.
© 2025 PatSnap. All rights reserved.Legal|Privacy policy|Modern Slavery Act Transparency Statement|Sitemap|About US| Contact US: help@patsnap.com