Rotary swaging forming method for automobile aluminum alloy wheel hubs
A technology for automobile wheels and aluminum alloys, which is applied to wheels, vehicle parts, metal processing equipment, etc., and can solve the problems of high energy consumption, complicated process, and high cost of forgings
- Summary
- Abstract
- Description
- Claims
- Application Information
AI Technical Summary
Problems solved by technology
Method used
Examples
Embodiment 1
[0013] (1) Material preparation: Calculate the volume of the required blank according to the wheel hub parts diagram, take the 15-inch wheel hub as an example, cut the semi-solid alloy thixotropic aluminum alloy bar material for the cylindrical forged hub into a blank with a diameter of 450mm;
[0014] (2) Cleaning: clean the billet to remove surface impurities such as oil stains;
[0015] (3) Blank preheating: heat the cut blank to 590°C in 30 minutes and keep it warm for 1 hour;
[0016] (4) Forging: Before forging work, preheat the mold to 450°C in 20 minutes, separate the upper mold and lower mold, spray lubricant on the working surface of the mold, and put the cylindrical aluminum alloy raw material blank that has been preheated at high temperature Put it into the mold, extrude with a 30MN forging press, and hold the pressure for 15s to make a forging blank;
[0017] (5) Flaring: Take out the above-mentioned forgings and put them into a small-tonnage flaring press to com...
Embodiment 2
[0020] (1) Material preparation: Taking the 18-inch wheel hub as an example, cut the semi-solid alloy thixotropic aluminum alloy bar stock for the cylindrical forged hub into a billet with a diameter of 600mm;
[0021] (2) Cleaning: clean the billet to remove surface impurities such as oil stains;
[0022] (3) Blank preheating: heat the cut blank to 595°C in 30 minutes and keep it warm for 1 hour;
[0023] (4) Forging: Before forging work, preheat the mold to 450°C in 20 minutes, separate the upper mold and lower mold, spray lubricant on the working surface of the mold, and put the cylindrical aluminum alloy raw material blank that has been preheated at high temperature Put it into the mold, extrude it with a 30MN forging press, and hold the pressure for 20s to make a forging blank;
[0024] (5) Flaring: Take out the above-mentioned forgings and put them into a small-tonnage flaring press to complete the above-mentioned forgings' flaring;
[0025] (6) Spinning forming: On th...
PUM
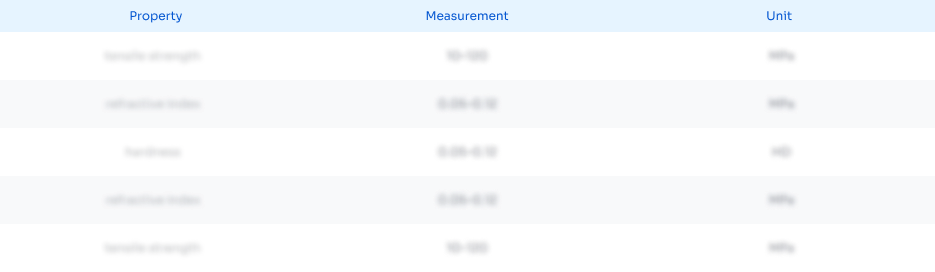
Abstract
Description
Claims
Application Information

- R&D
- Intellectual Property
- Life Sciences
- Materials
- Tech Scout
- Unparalleled Data Quality
- Higher Quality Content
- 60% Fewer Hallucinations
Browse by: Latest US Patents, China's latest patents, Technical Efficacy Thesaurus, Application Domain, Technology Topic, Popular Technical Reports.
© 2025 PatSnap. All rights reserved.Legal|Privacy policy|Modern Slavery Act Transparency Statement|Sitemap|About US| Contact US: help@patsnap.com