Anodization closing method for improving corrosion resistance of aluminum alloy
An aluminum alloy, anodizing technology, applied in the direction of anodic oxidation, electrolytic coating, surface reaction electrolytic coating, etc., can solve the problems of toxicity, human health and environmental hazards, achieve improved compactness, low input cost, and low equipment requirements high effect
- Summary
- Abstract
- Description
- Claims
- Application Information
AI Technical Summary
Problems solved by technology
Method used
Image
Examples
Embodiment 1
[0046] 1) Pretreatment of aluminum surface
[0047] a. Alkaline cleaning: Remove oil stains and adsorbed impurities on the surface of parts to obtain a clean surface. The alkaline washing uses heated NaOH solution, the specific parameters are 80g / L NaOH solution, the temperature is 90 °C, and the time is 3s after a large number of white bubbles appear on the entire surface.
[0048] b. Washing: take out the aluminum alloy from the alkali washing solution immediately after alkali washing, wash it with clean water, and remove the excess treatment liquid in time;
[0049] c. Pickling: HNO is used for pickling3 Solution, the specific parameters are 20% (mass ratio) HNO 3 The solution, room temperature, for 18 minutes, fully exposed and activated the substrate, and made the surface of the product bright.
[0050] d. Washing with water: Wash with clean water immediately after pickling, and remove excess treatment liquid in time to avoid excessive treatment and damage to the surfa...
Embodiment 2
[0071] 1) Pretreatment of aluminum surface
[0072] a. Alkaline cleaning: Remove oil stains and adsorbed impurities on the surface of parts to obtain a clean surface. The alkaline washing uses heated NaOH solution, the specific parameters are 100g / L NaOH solution, the temperature is 70 °C, and the time is 3s after a large number of white bubbles appear on the entire surface.
[0073] b. Washing: take out the aluminum alloy from the alkali washing solution immediately after alkali washing, wash it with clean water, and remove the excess treatment liquid in time;
[0074] c. Pickling: HNO is used for pickling 3 Solution, the specific parameters are the mass content of 20% HNO 3 Solution, room temperature, time 20 minutes, make the substrate fully exposed and activated, and make the surface of the product bright.
[0075] d. Washing with water: Wash with clean water immediately after pickling, and remove excess treatment liquid in time to avoid excessive treatment and damage ...
Embodiment 3
[0096] 1) Pretreatment of aluminum surface
[0097] a. Alkaline cleaning: Remove oil stains and adsorbed impurities on the surface of parts to obtain a clean surface. The alkaline washing uses heated NaOH solution, the specific parameters are 90g / L NaOH solution, the temperature is 70 °C, and the time is 3s after a large number of white bubbles appear on the entire surface.
[0098] b. Washing: take out the aluminum alloy from the alkali washing solution immediately after alkali washing, wash it with clean water, and remove the excess treatment liquid in time;
[0099] c. Pickling: HNO is used for pickling 3 Solution, the specific parameters are the mass content of 20% HNO 3 Solution, room temperature, time 2 minutes, make the substrate fully exposed and activated, and make the surface of the product bright.
[0100] d. Washing with water: Wash with clean water immediately after pickling, and remove excess treatment liquid in time to avoid excessive treatment and damage to...
PUM
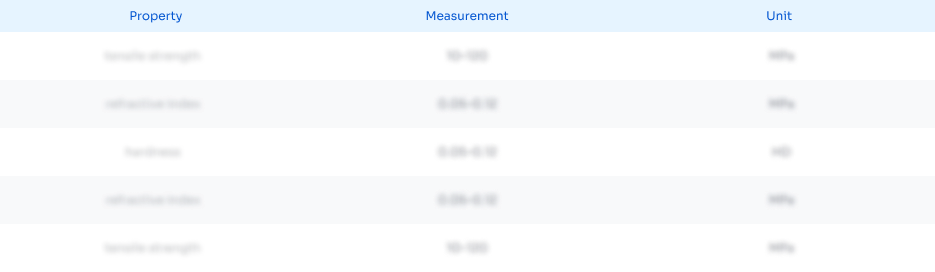
Abstract
Description
Claims
Application Information

- Generate Ideas
- Intellectual Property
- Life Sciences
- Materials
- Tech Scout
- Unparalleled Data Quality
- Higher Quality Content
- 60% Fewer Hallucinations
Browse by: Latest US Patents, China's latest patents, Technical Efficacy Thesaurus, Application Domain, Technology Topic, Popular Technical Reports.
© 2025 PatSnap. All rights reserved.Legal|Privacy policy|Modern Slavery Act Transparency Statement|Sitemap|About US| Contact US: help@patsnap.com