Composite film for medicine packaging, and making method thereof
A packaging and composite film technology, applied in the field of pharmaceutical packaging, can solve the problems of high cost of glass glue and difficult to open packaging bags, etc., and achieve the effect of high peel strength, good heat sealing performance, and tight composite
- Summary
- Abstract
- Description
- Claims
- Application Information
AI Technical Summary
Problems solved by technology
Method used
Image
Examples
Embodiment 1
[0023] A 1100mm wide gravure rotary high-speed printing machine is used to add benzene and ketone-free inks for printing; the non-printing surface of the aluminum foil is coated with a screen roll as a coating roll, coated with a two-component polyurethane resin glue, and then passed through 50 ° C, Dry the solvent in a three-stage oven at 60°C and 70°C, enter the composite roller and polyethylene film, and then wind up to form a composite semi-finished product; put the above composite semi-finished product in a curing room at 50°C for 36 hours; put the composited The packaging film is cut into roll film with a 1000mm wide slitting machine; the cut roll film is made into a center seal bag or a three side seal bag or other Shaped bag.
[0024] The composite film for pharmaceutical packaging prepared in this example has clear layers, beautiful appearance, pressure resistance, compact composite, no blistering, no rupture, high peel strength, good heat sealing performance, and goo...
Embodiment 2
[0026] A 1100mm wide gravure rotary high-speed printing machine is used to add benzene and ketone-free inks for printing; the non-printing surface of the aluminum foil is coated with a screen roll as a coating roll, and coated with a two-component polyurethane resin glue. Dry the solvent in a three-stage oven at 65°C and 75°C, enter the composite roll and heat the polyethylene film, and then wind up to form a composite semi-finished product; put the above composite semi-finished product in a curing room at 55°C for 48 hours; put the composited The packaging film is cut into roll film with a 1000mm wide slitting machine; the cut roll film is made into a center seal bag or a three side seal bag or other Shaped bag.
[0027] The composite film for pharmaceutical packaging prepared in this example has clear layers, beautiful appearance, pressure resistance, compact composite, no blistering, no rupture, high peel strength, good heat sealing performance, and good tearability and eas...
Embodiment 3
[0029] A 1100mm wide gravure rotary high-speed printing machine is used to add benzene and ketone-free inks for printing; the non-printing surface of the aluminum foil is coated with a screen roll as a coating roll, and coated with a two-component polyurethane resin glue. Dry the solvent in a three-stage oven at 70°C and 80°C, enter the composite roll and heat the polyethylene film, and then wind up to form a composite semi-finished product; put the above composite semi-finished product in a curing room at 60°C for 60 hours; put the composited The packaging film is cut into roll film with a 1000mm wide slitting machine; the cut roll film is made into a center seal bag or a three side seal bag or other Shaped bag.
[0030] The composite film for pharmaceutical packaging prepared in this example has clear layers, beautiful appearance, pressure resistance, compact composite, no blistering, no rupture, high peel strength, good heat sealing performance, and good tearability and eas...
PUM
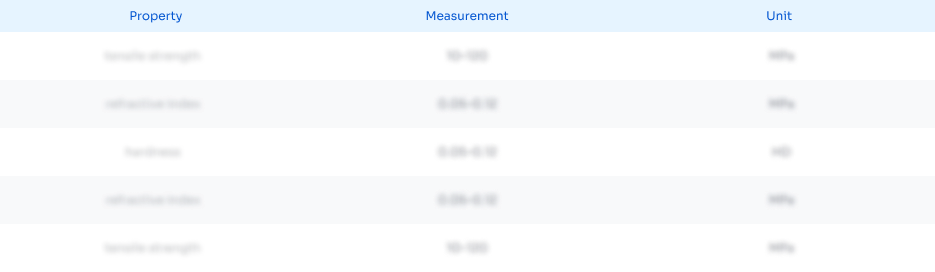
Abstract
Description
Claims
Application Information

- R&D Engineer
- R&D Manager
- IP Professional
- Industry Leading Data Capabilities
- Powerful AI technology
- Patent DNA Extraction
Browse by: Latest US Patents, China's latest patents, Technical Efficacy Thesaurus, Application Domain, Technology Topic, Popular Technical Reports.
© 2024 PatSnap. All rights reserved.Legal|Privacy policy|Modern Slavery Act Transparency Statement|Sitemap|About US| Contact US: help@patsnap.com