Method of guaranteeing hardness of welded closed impeller after welding
A closed impeller, post-welding technology, applied in the field of ensuring the hardness of the welded closed impeller after welding, can solve the problems of low bearing capacity, difficulty in meeting military products, and excessive blade distortion rate
- Summary
- Abstract
- Description
- Claims
- Application Information
AI Technical Summary
Problems solved by technology
Method used
Examples
Embodiment Construction
[0011] Taking the processing of the upper closed impeller of a turbine cooler as an example, when the impeller is not processed by the method described in the present invention, heat treatment is used after salt bath brazing to meet the hardness requirements of the components, but in the actual process, After the first heat treatment, it was found that the hardness of the impeller did not meet the requirements, and its HB≤100, so the second heat treatment was carried out. After the second heat treatment, it was found that the impeller material had cracks. In order to solve the above problems, the method for ensuring the post-welding hardness of the welded closed impeller according to the present invention is adopted. After the aluminum alloy closed impeller on a certain turbo cooler is subjected to conventional machining and welding, the parts are taken out from the salt bath furnace. Put it into boiling water at 100°C within 2 minutes for 30 minutes of frying salt treatment, t...
PUM
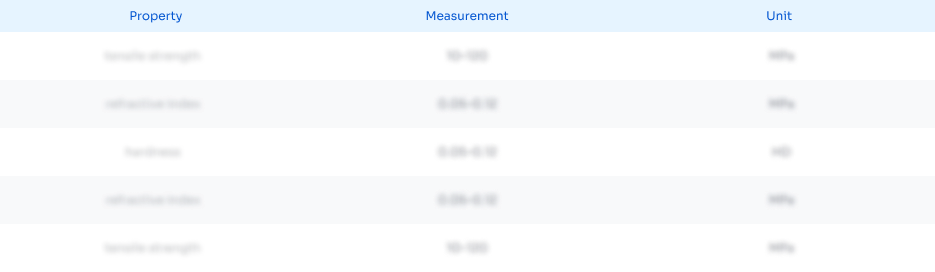
Abstract
Description
Claims
Application Information

- R&D Engineer
- R&D Manager
- IP Professional
- Industry Leading Data Capabilities
- Powerful AI technology
- Patent DNA Extraction
Browse by: Latest US Patents, China's latest patents, Technical Efficacy Thesaurus, Application Domain, Technology Topic, Popular Technical Reports.
© 2024 PatSnap. All rights reserved.Legal|Privacy policy|Modern Slavery Act Transparency Statement|Sitemap|About US| Contact US: help@patsnap.com