Improved production method of multi-color patterned roller-coated steel plate
A production method and pattern roller technology, which are applied to equipment, coating, general parts of printing machinery, etc. using the electrical recording process of charge patterns, can solve the problem that the transfer of steel belt roll coating and the adjacent roll coating unit cannot be realized. Continuous production, inconsistent speed and other problems, to achieve the effect of improving production efficiency
- Summary
- Abstract
- Description
- Claims
- Application Information
AI Technical Summary
Problems solved by technology
Method used
Image
Examples
Embodiment 1
[0031] like figure 1As shown, the present embodiment provides a production method of a two-color pattern color steel plate, comprising the following steps: A. Prepare the steel strip to be printed, and in this step, use an uncoiler to uncoil the steel coil and perform edge trimming and stitching Machine stitches the uncoiled steel strip; B. Performs pretreatment on the steel strip to be printed; C. Uses the first roller coating unit to perform a roll coating transfer on the steel strip to be printed; D. Specific time Adopt the second roller coating unit to carry out secondary roller coating transfer to the steel strip; E. carry out post-treatment of spraying bright varnish to the steel strip; In the step C, adopt the servo control system to coat the first roller The unit is controlled, and the control process of the servo control system is, see image 3 :
[0032] S1, input the roll diameter and the process speed of each roller in the first roller coating unit into the PLC ...
Embodiment 2
[0045] In this embodiment, a structure of the roller coating transfer unit used in step B and step C in embodiment 1 is provided. For the specific structure, see figure 2 , the roller coating unit includes feeding equipment 1 for providing coating; suction roller 2, whose peripheral surface is connected with the feeding equipment 1, and has an image area formed when filling with the coating on the peripheral surface a plurality of depressions; the rubber coating roller 3, whose peripheral surface is connected with the suction roller 2, is used to accept the image area formed by the coating on the coating roller 3, and transfer the image area onto the steel plate; also includes a first scraper 4, installed on the first scraper bracket, contacting the suction roller 2 at a specific angle, for scraping off the paint outside the image area of the suction roller 2 The second scraper 5, installed on the second scraper bracket, is in contact with the coating roller 2 at a specif...
PUM
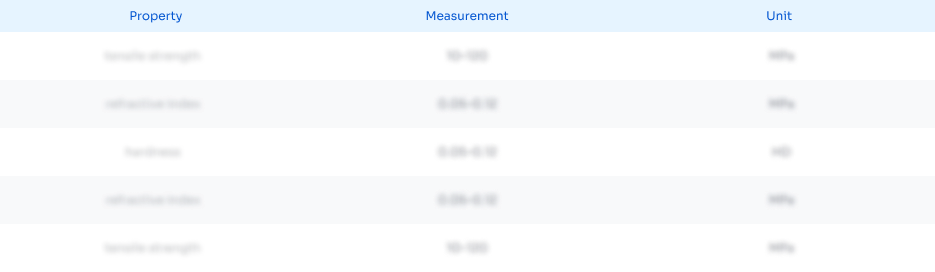
Abstract
Description
Claims
Application Information

- R&D
- Intellectual Property
- Life Sciences
- Materials
- Tech Scout
- Unparalleled Data Quality
- Higher Quality Content
- 60% Fewer Hallucinations
Browse by: Latest US Patents, China's latest patents, Technical Efficacy Thesaurus, Application Domain, Technology Topic, Popular Technical Reports.
© 2025 PatSnap. All rights reserved.Legal|Privacy policy|Modern Slavery Act Transparency Statement|Sitemap|About US| Contact US: help@patsnap.com