Rotary shear flow tray
A rotary shearing, tray technology, applied in chemical/physical/physical chemical processes, dispersed particle separation, fractionation, etc., can solve the problems of low tray efficiency, short residence time, insufficient gas-liquid contact, etc. The effect of mass transfer driving force, reducing gas film and liquid film resistance, and accelerating renewal
- Summary
- Abstract
- Description
- Claims
- Application Information
AI Technical Summary
Problems solved by technology
Method used
Image
Examples
Embodiment 1
[0023] Embodiment 1 The rotary shear flow tray of the present invention includes a tray 1, on which a plurality of downcomers 11 and a plurality of spray holes 12 are arranged, and one end of the downcomer 11 is fixed On the outer ring of the tray 1, the other end extends toward the center of the tray 1 until it communicates with the central liquid collection pipe 13 below the tray 1. The liquid outlet of the central liquid collection pipe 13 is connected to the In the liquid receiving tank 14 below the liquid pipe 13, the downcomer 11 is arranged along the circumference of the tray 1 to form a circle of downcomer rings, and the downcomer 11 is fixed on the One end of the tray 1 is higher than the upper surface of the tray 1; the liquid receiving tank 14 is connected with the central liquid collecting pipe 13 through the lacing plate 15, and the outlet of the central liquid collecting pipe and the overflow port of the liquid receiving tank are used The liquid level difference ...
Embodiment 2
[0034] Embodiment 2 The difference between this embodiment and Embodiment 1 is that the inclined injection holes can be tongue-shaped injection holes, and the rest of the implementation methods and structures are the same, taking the existing injection tray as an example (assuming all Macro-quantitative analysis based on a tray with a tower body diameter of 1 meter): deducting the liquid receiving area and the downcomer area, the longest path for the liquid to flow on the tray from the liquid receiving area to the downcomer area is about 0.75 meters, while The path length of the liquid from the liquid receiving area to the downcomer of the rotating shear flow tray is the sum of the concentric circular paths flowing between the liquid receiving area (tray central area) and the downcomer, that is It is about 10-15 meters, that is, the gas-liquid mass transfer time can be increased by more than ten times, and the number of circular paths n is determined by the number and arrangem...
PUM
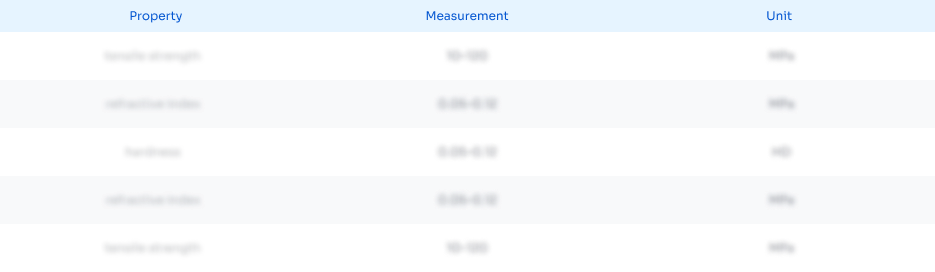
Abstract
Description
Claims
Application Information

- R&D Engineer
- R&D Manager
- IP Professional
- Industry Leading Data Capabilities
- Powerful AI technology
- Patent DNA Extraction
Browse by: Latest US Patents, China's latest patents, Technical Efficacy Thesaurus, Application Domain, Technology Topic, Popular Technical Reports.
© 2024 PatSnap. All rights reserved.Legal|Privacy policy|Modern Slavery Act Transparency Statement|Sitemap|About US| Contact US: help@patsnap.com