Manufacture method of stainless steel screw
A manufacturing method, stainless steel technology, applied in the direction of screws, threaded fasteners, connecting components, etc., can solve the problems of unable to cut normally, wide kerf, etc.
- Summary
- Abstract
- Description
- Claims
- Application Information
AI Technical Summary
Problems solved by technology
Method used
Examples
Embodiment Construction
[0010] The invention is a method for manufacturing stainless steel. It is a base material that is low-carbon steel or low-carbon alloy steel, and is pre-forged or cut into a round rod with a shoulder and an unthreaded shank or a drill tail. The threaded austenitic stainless steel round rod with head is joined together by welding, then the welding burr and the shoulder of the carburized steel part are cut to form a non-carburized hardened zone of appropriate width, and finally the thread rolling process and Quenching treatment is used to manufacture a connection between the head and the threaded shank, which has excellent corrosion resistance. The tail has austenitic stainless steel self-tapping and self-drilling screws suitable for self-tapping and self-drilling functions.
PUM
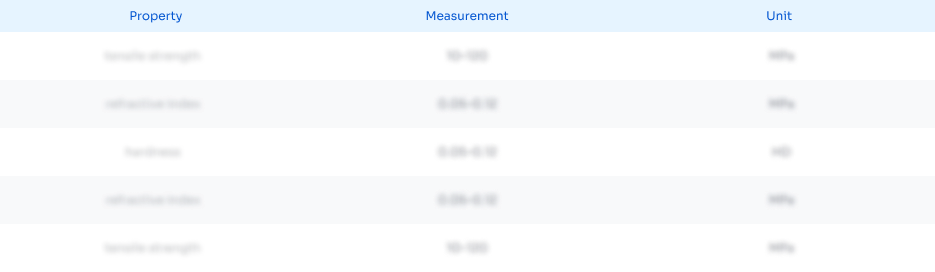
Abstract
Description
Claims
Application Information

- R&D Engineer
- R&D Manager
- IP Professional
- Industry Leading Data Capabilities
- Powerful AI technology
- Patent DNA Extraction
Browse by: Latest US Patents, China's latest patents, Technical Efficacy Thesaurus, Application Domain, Technology Topic, Popular Technical Reports.
© 2024 PatSnap. All rights reserved.Legal|Privacy policy|Modern Slavery Act Transparency Statement|Sitemap|About US| Contact US: help@patsnap.com