Method for treatment and resource utilization of sludge based on low-pressure catalytic thermal hydrolysis and application of method
A catalytic thermal hydrolysis and sludge technology, applied in water/sludge/sewage treatment, sludge treatment, dehydration/drying/thickened sludge treatment, etc., can solve the problem that dehydrated cake cannot be directly used as biomass fuel, Problems such as high equipment cost and low treatment efficiency can achieve the effect of improving anaerobic digestion performance, dehydration performance and reducing tail gas treatment load
- Summary
- Abstract
- Description
- Claims
- Application Information
AI Technical Summary
Problems solved by technology
Method used
Image
Examples
Embodiment 1
[0044] like figure 2 As shown, inject 1 ton of sludge with a water content of 85-90% and 50kg of sodium carbonate into the reactor, close the feed port of the reactor, and start the stirring device in the reactor; Inject saturated steam of 1.0-1.1MPa to heat the sludge mixed with sodium carbonate in the reactor; detect the real-time temperature of the sludge in the lower part of the reactor, and when the temperature of the sludge reaches 170°C, stop injecting saturated steam and keep 20- 25 minutes; then open the pressure relief valve and start to exhaust steam and pressure relief, when the pressure in the reactor drops below 0.05MPa, open the discharge valve to discharge the mud obtained by thermal hydrolysis treatment; after the mud is cooled, carry out mechanical dehydration to obtain dehydration respectively. The dehydrated cake with liquid and water content of 45-50%; the removed liquid is further anaerobic digestion reaction to prepare biogas. At this point, the compre...
Embodiment 2
[0046] like image 3 As shown, inject 1 ton of sludge with a water content of 80-85% and 15kg of sodium hydroxide into the reactor, close the feed port of the reactor, and start the stirring device in the reactor; stir at a constant speed for 1 minute to make the sodium hydroxide and The sludge is mixed evenly; the saturated steam of 1.1-1.2MPa is injected into the reactor from the upper and lower parts of the reactor at the same time, and the sludge mixed with sodium hydroxide in the reactor is heated; the sludge in the middle of the reactor is detected in real time When the sludge temperature reaches 180°C, stop injecting saturated steam and keep it for 15-20 minutes; then open the pressure relief valve to start exhausting and pressure relief, and open the discharge valve when the pressure in the reactor drops below 0.05MPa. Discharge the mud obtained from the thermal hydrolysis treatment; mechanically dehydrate the mud after cooling to obtain the dehydrated liquid and dehyd...
Embodiment 3
[0048] Inject 1 ton of sludge with a moisture content of 75-80% and 20kg of potassium hydroxide into the reactor, close the feed port of the reactor, and start the stirring device in the reactor; stir at a constant speed for 3 minutes to mix potassium hydroxide with the sludge Uniform; inject saturated steam of 1.2-1.3MPa from the steam boiler from the upper part of the reactor to heat the sludge mixed with potassium hydroxide in the reactor; detect the real-time temperature of the sludge in the lower part of the reactor, when the sludge temperature When it reaches 140°C, stop injecting saturated steam and keep it for 15-20 minutes; then open the pressure relief valve to start steam and pressure relief, and when the pressure in the reactor drops below 0.05MPa, open the discharge valve and discharge the thermal hydrolysis treatment to obtain The mud; after the mud is cooled, it is mechanically dehydrated to obtain the dewatered cake with a water content of 40-45% respectively; ...
PUM
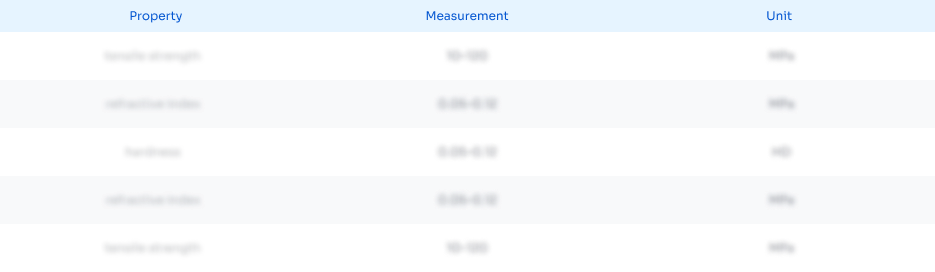
Abstract
Description
Claims
Application Information

- Generate Ideas
- Intellectual Property
- Life Sciences
- Materials
- Tech Scout
- Unparalleled Data Quality
- Higher Quality Content
- 60% Fewer Hallucinations
Browse by: Latest US Patents, China's latest patents, Technical Efficacy Thesaurus, Application Domain, Technology Topic, Popular Technical Reports.
© 2025 PatSnap. All rights reserved.Legal|Privacy policy|Modern Slavery Act Transparency Statement|Sitemap|About US| Contact US: help@patsnap.com