Production method for fuel ethanol
A production method and technology for fuel ethanol, which are applied in microorganism-based methods, biochemical equipment and methods, biofuels, etc., can solve the problem of low ethanol concentration, and achieve the goal of improving ethanol yield, shortening process flow, and improving production efficiency. Effect
- Summary
- Abstract
- Description
- Claims
- Application Information
AI Technical Summary
Problems solved by technology
Method used
Examples
Embodiment 1
[0026] Example 1 (comparative scheme) separate fermentation of corn stalks
[0027] Add 2 L of tap water, 0.4 kg of steam explosion pretreated corn stalks, and 50 g of yeast powder into a 5 L fermenter to adjust the pH to 5.0. At the same time, 800 mL of YPD culture was prepared in a 3 L Erlenmeyer flask, sterilized, inoculated with FE-B yeast, and cultured overnight.
[0028] Add 200 mL of cellulase to a 5 L fermenter, and insert 800 mL of yeast cultured overnight. Simultaneous saccharification and fermentation were carried out at 42°C. At 24h, 48h, 72h and 96h, 0.2 kg of steam explosion pretreated corn stalks were added, and the ethanol concentration in the system was 8.2 wt% (weight percentage) after 120 hours.
Embodiment 2
[0029] Embodiment 2 (comparative scheme) acorn is fermented separately
[0030] Take 1.2 kg of acorn powder and add 3L of tap water into a double-layer glass reactor (5L), use the interlayer to keep the temperature of the system at 50°C, extract for 24 hours, and centrifuge. The solid residue is washed once with an equal volume of hot water, and then Centrifuge. The washed solid slag was mixed with water below 50°C to prepare an emulsion, the solid content of the emulsion was 34wt%, and a certain amount of 10wt% dilute lye was added under constant stirring to make the pH of the emulsion reach 5.8. Add Novozymes Liquozyme Supra / 2.2x Amylase 0.464 g. Liquefied at 95°C for 1 hour, the measured DX value of the liquefied liquid was 15%. Then lower the temperature, adjust the pH to 4.5, add 0.387 g of Suhong GA 475 glucoamylase from Novozymes, and saccharify at 58°C for 48 h. The DX value in the saccharified feed solution is measured to be 65%. Then, 0.05% dry weight yeast was...
Embodiment 3
[0031] Example 3 (comparative scheme) co-fermentation of corn stalks and acorn powder
[0032] A double-layer glass reactor (10 L) was added with 1.2 kg of acorn powder and 1 kg of steam explosion pretreated corn stalk, 5.5 L of tap water, and a certain amount of 10wt% dilute lye was added under constant stirring to make the pH of the emulsion reach 5.8. Add Novozymes Liquozyme Supra / 2.2x Amylase 0.464 g. Liquefy at 95°C for 1 hour, then lower the temperature, adjust the pH to 4.5, pour into a 10L fermenter, add 50 g of yeast powder, 200 mL of cellulase and 0.387 g of Novozymes’ Suhong GA 475 starch glucoamylase at 50°C for enzymatic hydrolysis 48h. At the same time, 800 mL of YPD culture was prepared in a 3 L Erlenmeyer flask, sterilized, inoculated with FE-B yeast, cultured overnight, and put into the above-mentioned 10L fermenter as seeds, cultured at 36 °C for 24 h, and then cultured at 42 °C for 48 h. The ethanol concentration in the fermentation broth was 8.5 wt%. ...
PUM
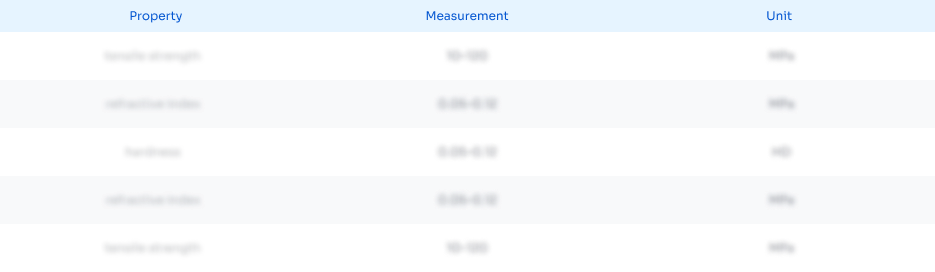
Abstract
Description
Claims
Application Information

- R&D
- Intellectual Property
- Life Sciences
- Materials
- Tech Scout
- Unparalleled Data Quality
- Higher Quality Content
- 60% Fewer Hallucinations
Browse by: Latest US Patents, China's latest patents, Technical Efficacy Thesaurus, Application Domain, Technology Topic, Popular Technical Reports.
© 2025 PatSnap. All rights reserved.Legal|Privacy policy|Modern Slavery Act Transparency Statement|Sitemap|About US| Contact US: help@patsnap.com