Composite material and lithium ion battery plastic shell made of the same
A composite material and mixture technology, used in battery pack parts, circuits, electrical components, etc., can solve the problems of reduced battery performance, insufficient, poor sealing, etc., and achieve the effect of strong toughness and impact resistance.
- Summary
- Abstract
- Description
- Claims
- Application Information
AI Technical Summary
Problems solved by technology
Method used
Image
Examples
Embodiment 1
[0021] The preparation method of composite material: the steps are as follows,
[0022] (1) Mix and stir 80 parts by weight of polypropylene, 15 parts of high-density polyethylene and 5 parts of lubricant until uniform;
[0023] (2) Put the uniformly stirred mixture into a screw extruder for melt mixing for 2-4 minutes, the screw temperature is 145°C-210°C, and the screw speed is 200-300 rpm.
[0024] The lithium-ion battery plastic casing made of composite materials, the manufacturing steps are as follows:
[0025] The composite material prepared according to the above method is blended with the acid and alkali resistant color masterbatch in proportion, baked, and then injected through an injection mold. Use a horizontal mixer to stir at a constant speed for 5-10 minutes to disperse the color masterbatch in the raw materials evenly; bake the mixed raw materials at 75°C for 2 hours before hot injection molding;
[0026] The hot injection molding conditions are: injection mol...
Embodiment 2
[0028] The preparation method of composite material: the steps are as follows,
[0029] (1) Mix and stir 86 parts by weight of polypropylene, 10 parts of high-density polyethylene and 4 parts of lubricant until uniform;
[0030] (2) Put the uniformly stirred mixture into a screw extruder for melt mixing for 2-4 minutes, the screw temperature is 145°C-210°C, and the screw speed is 200-300 rpm.
[0031] The lithium-ion battery plastic casing made of composite materials, the manufacturing steps are as follows:
[0032] The composite material prepared according to the above method is blended with the acid and alkali resistant color masterbatch in proportion, baked, and then injected through an injection mold. Use a horizontal mixer to stir at a constant speed for 5-10 minutes to disperse the color masterbatch in the raw materials evenly; bake the mixed raw materials at 75°C for 2 hours before hot injection molding;
[0033] The hot injection molding conditions are: injection mol...
Embodiment 3
[0035] The preparation method of composite material: the steps are as follows,
[0036] (1) Mix and stir 90 parts by weight of polypropylene, 7 parts of high-density polyethylene and 3 parts of lubricant until uniform;
[0037] (2) Put the uniformly stirred mixture into a screw extruder for melt mixing for 2-4 minutes, the screw temperature is 145°C-210°C, and the screw speed is 200-300 rpm.
[0038] The lithium-ion battery plastic casing made of composite materials, the manufacturing steps are as follows:
[0039] The composite material prepared by the method according to claim 4 is blended with the acid and alkali resistant color masterbatch in proportion, baked, and then injected through an injection mold. Use a horizontal mixer to stir at a constant speed for 5-10 minutes to disperse the color masterbatch in the raw materials evenly; bake the mixed raw materials at 75°C for 2 hours before hot injection molding;
[0040] The hot injection molding conditions are: injection...
PUM
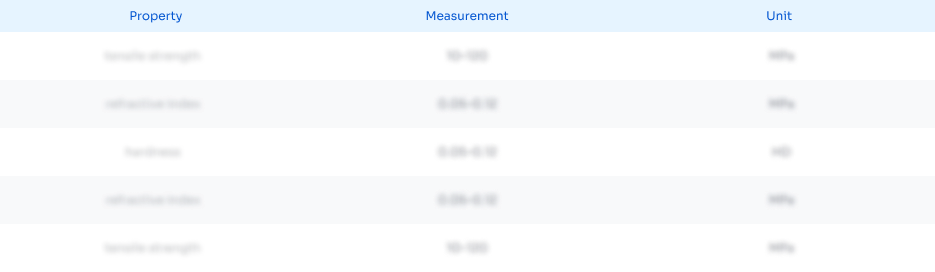
Abstract
Description
Claims
Application Information

- R&D
- Intellectual Property
- Life Sciences
- Materials
- Tech Scout
- Unparalleled Data Quality
- Higher Quality Content
- 60% Fewer Hallucinations
Browse by: Latest US Patents, China's latest patents, Technical Efficacy Thesaurus, Application Domain, Technology Topic, Popular Technical Reports.
© 2025 PatSnap. All rights reserved.Legal|Privacy policy|Modern Slavery Act Transparency Statement|Sitemap|About US| Contact US: help@patsnap.com