Colored flame-retardant insulation vulcanized fiber board and manufacturing technique thereof
A flame retardant, steel board technology, applied in paper, papermaking, textiles and paper making, etc., can solve the problems of inability to produce color flame retardant insulating steel board, can not meet the needs of the electrical industry, etc., achieve good machining performance, easy to use. Control, the effect of low production cost
- Summary
- Abstract
- Description
- Claims
- Application Information
AI Technical Summary
Problems solved by technology
Method used
Image
Examples
example 1
[0031] 1. The chemically bleached wood pulp fibers prepared by the kraft method are fibrously beaten, and the beating degree of the wood pulp fibers is beaten to 45 ° SR. Then add zinc borate inorganic flame retardant and fully mix with wood pulp fiber in beating equipment, the mixing ratio of wood pulp fiber and zinc borate inorganic flame retardant is 6: 4, and concentration is 5%;
[0032] 2. Add 4000kg of the above-mentioned prepared slurry (concentration 5%) and 5kg of direct magenta dye in the slurry tank. After the slurry and the dye are fully mixed, add 10kg of aluminum sulfate solution (concentration 10%) to adjust the concentration of the slurry. The pH value is 4.5-5;
[0033] 3. Prepare polyvinyl alcohol and melamine formaldehyde resin into solutions with a concentration of 5%, and then mix them uniformly according to a ratio of 1:1, and then dilute to a concentration of 1% for later use;
[0034] 4. Extract 1000kg of the above-mentioned mixed slurry from the slur...
example 2
[0040] 1. The chemically bleached wood pulp fibers prepared by the kraft method are fibrously beaten, and the beating degree of the wood pulp fibers is beaten to 35 ° SR. White office waste paper is fiberized and beaten with beating equipment, and the beating degree of waste paper pulp is beaten to 55°SR
[0041] 2. Add above-mentioned beaten wood pulp fiber (concentration 5%) in the pulping tank, white office waste paper (concentration 5%), zinc borate inorganic flame retardant (powder) fully mix, wood pulp fiber (concentration 5%) %), white office waste paper (concentration 5%), the mixing ratio of zinc borate inorganic flame retardant (powder) is 5: 1: 4;
[0042] 3. Add 4000kg of the above-mentioned prepared slurry (concentration 5%) in the slurry tank, 3kg of direct red dye, 3kg of direct yellow dye, after the slurry and the dye are fully mixed, add 10kg of aluminum sulfate solution (concentration 10%), Adjust the pH value of the slurry at 4.5-5;
[0043] Prepare polyvi...
example 3
[0050] 1. The chemical natural color wood pulp fiber prepared by the sulfate method is subjected to fibrosis and beating treatment with a beating equipment, and the beating degree of the wood pulp fiber is beaten to 45°SR; to 35°SR;
[0051] 2. Add above-mentioned beaten wood pulp fiber (concentration 5%) in the pulping tank, waste kraft card secondary fiber (concentration 5%), zinc borate inorganic flame retardant (powder) fully mix, wood pulp fiber ( Concentration 5%), waste kraft card secondary fiber (concentration 5%), the mixing ratio of zinc borate inorganic flame retardant (powder) is 2: 5: 3;
[0052] 3. Add 4000kg of the above-mentioned prepared slurry (concentration: 5%) and 10kg of direct sun-fast black dye to the slurry tank. After the slurry and the dye are fully mixed, add 10kg of aluminum sulfate solution (concentration: 10%) to adjust the slurry The pH value is 4.5-5;
[0053] 3. Prepare polyvinyl alcohol and melamine formaldehyde resin into solutions with a ...
PUM
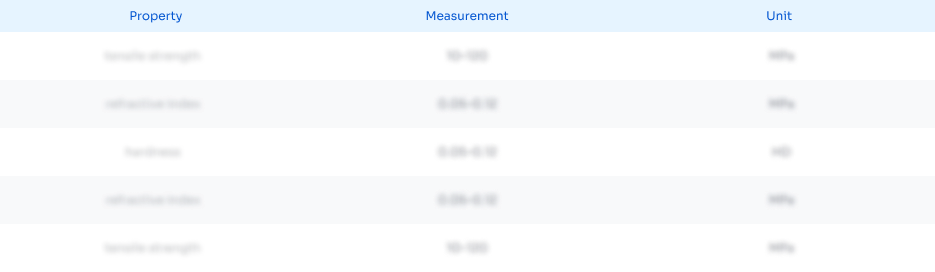
Abstract
Description
Claims
Application Information

- Generate Ideas
- Intellectual Property
- Life Sciences
- Materials
- Tech Scout
- Unparalleled Data Quality
- Higher Quality Content
- 60% Fewer Hallucinations
Browse by: Latest US Patents, China's latest patents, Technical Efficacy Thesaurus, Application Domain, Technology Topic, Popular Technical Reports.
© 2025 PatSnap. All rights reserved.Legal|Privacy policy|Modern Slavery Act Transparency Statement|Sitemap|About US| Contact US: help@patsnap.com