Burning process and burning boiler for processing high-density saliferous organic wastewater
A high-concentration salt-containing and organic waste liquid technology, applied in incinerators, steam boilers, combustion methods, etc., can solve problems that are not conducive to controlling the temperature of the combustion area, not conducive to controlling the burnout of waste liquid, and incomplete combustion of waste liquid , to achieve the effect of continuous and stable operation cycle, excellent treatment effect and fast burning speed
- Summary
- Abstract
- Description
- Claims
- Application Information
AI Technical Summary
Problems solved by technology
Method used
Image
Examples
Embodiment Construction
[0025] In order to make the object, technical solution and advantages of the present invention clearer, the present invention will be further described in detail below with reference to the accompanying drawings and examples.
[0026] Such as figure 1 As shown, the environmentally friendly incineration boiler for treating high-concentration salt-containing organic waste liquid of the present invention includes a downward adiabatic furnace 5, a multi-stage radiation cooling chamber 6, 12, a convective heat exchange chamber 13, a soot blowing device 15, a steam-water outlet pipe 17 and The steam drum 18, the descending adiabatic furnace 5, the multi-stage radiation cooling chambers 6, 12 and the convective heat exchange chamber 13 are connected in sequence, between the descending adiabatic furnace 5 and the first-stage radiation cooling chamber 6, the radiation cooling chambers 6, 12, and between the last-stage radiation cooling chamber 12 and the convection heat exchange chambe...
PUM
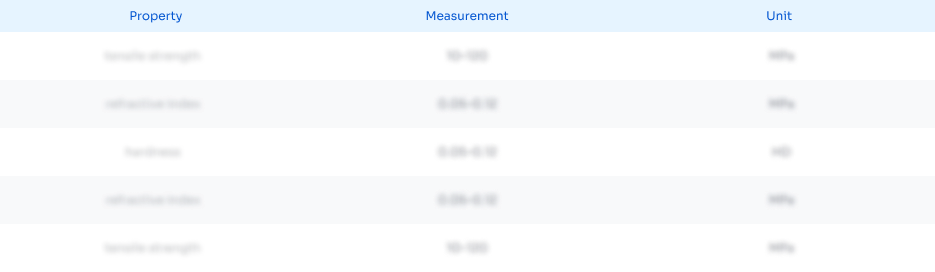
Abstract
Description
Claims
Application Information

- R&D
- Intellectual Property
- Life Sciences
- Materials
- Tech Scout
- Unparalleled Data Quality
- Higher Quality Content
- 60% Fewer Hallucinations
Browse by: Latest US Patents, China's latest patents, Technical Efficacy Thesaurus, Application Domain, Technology Topic, Popular Technical Reports.
© 2025 PatSnap. All rights reserved.Legal|Privacy policy|Modern Slavery Act Transparency Statement|Sitemap|About US| Contact US: help@patsnap.com