Method for recovering chloromethane from chloromethane-containing waste gas in maltol production
A technology for methyl chloride and maltol, which is applied in the field of recovering methyl chloride from methyl chloride-containing waste gas in the production of maltol, can solve problems such as unfriendly environment, and achieve the effects of reducing air pollution, effective recovery and treatment, and stable product quality.
- Summary
- Abstract
- Description
- Claims
- Application Information
AI Technical Summary
Problems solved by technology
Method used
Image
Examples
Embodiment 1
[0022] see figure 1 , the present invention is a process for recovering methyl chloride from methane chloride waste gas produced in the production process of maltol, including the following steps: (1) primary alkali washing: the vent pipe of the chlorination hydrolysis kettle and the secondary receiving tank for methanol recovery The emptying pipe of the outlet is connected to the middle and lower part of the primary alkali washing tower 1, and all waste gas generated during the reaction is collected into the alkali washing tower 1, and 800~1500L liquid caustic soda with a concentration of 10% or more is placed in the alkali washing tower 1. The liquid pump pumps the lye from the bottom to the top, sprays from top to bottom, and cleans the exhaust gas from bottom to top; (2) Buffer tank 2 collection: the gas after preliminary alkali washing is used in a large buffer tank 2 For collection, the size of the buffer tank 2 should be determined according to the specific air flow; (3...
Embodiment 2
[0025] Similar to Example 1, all waste gas generated by chlorination hydrolysis high-temperature rearrangement is collected into the primary alkali washing tower, and 15% lye is used for alkali washing. When the concentration of lye drops to 12%, the concentration of 100L of replacement is 31%. lye; the gas after preliminary alkali washing enters the buffer tank, using 30m 3 The buffer tank can recover 2 tons of methyl chloride a day; use Roots blower to pump the gas in the buffer tank to the water washing tower for washing, and replace the clean water every 2 hours; use concentrated sulfuric acid for two-stage pickling, the concentration of the first-stage sulfuric acid is at More than 80%; and then go through two-stage caustic soda for alkali washing to remove residual acidic substances and water. After being compressed by the gas compression body, it enters the condenser to be cooled into a liquid phase and then sent to the finished product storage tank.
Embodiment 3
[0027] Similar to Examples 1 and 2, the difference is that 18% lye is used for alkaline washing, and the results also meet the requirements of the first-class product of the chemical industry standard HG / T 3674-2000 of the People's Republic of China.
PUM
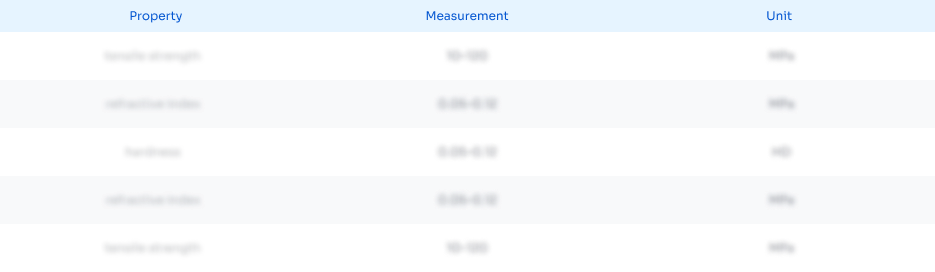
Abstract
Description
Claims
Application Information

- R&D
- Intellectual Property
- Life Sciences
- Materials
- Tech Scout
- Unparalleled Data Quality
- Higher Quality Content
- 60% Fewer Hallucinations
Browse by: Latest US Patents, China's latest patents, Technical Efficacy Thesaurus, Application Domain, Technology Topic, Popular Technical Reports.
© 2025 PatSnap. All rights reserved.Legal|Privacy policy|Modern Slavery Act Transparency Statement|Sitemap|About US| Contact US: help@patsnap.com