Die
A technology of mold and mold body, which is applied in the field of mold casting, can solve the problems of high dross content in castings, low yield rate, failure to reach and other problems, and achieve the effect of improving casting quality, improving wear resistance, and increasing yield rate
- Summary
- Abstract
- Description
- Claims
- Application Information
AI Technical Summary
Problems solved by technology
Method used
Image
Examples
Embodiment Construction
[0019] Such as figure 1 , figure 2 , image 3 , Figure 4 and Figure 5 As shown, a mold includes a mold body 5 composed of a lower mold 2 with a hemispherical cavity 1 inside and an upper mold 4 with a hemispherical curved surface cavity 3 inside, and a thermal insulation cavity that is arranged on the upper mold 4 and communicates with the outside world. 6, and the thermal insulation mold body 7 embedded in the thermal insulation cavity 6, the thermal insulation cavity 6 communicates with the hemispherical surface cavity 3, and an annular stepped groove 8 is set at the entrance of the thermal insulation cavity 6, and the thermal insulation mold body 7 The outer edge is provided with an annular flange 9 matching with the annular stepped groove 8, and a runner 10 is opened on the upper side of the upper mold 4, and the runner 10 passes through the channel 11 provided in the heat preservation mold body 7 and the upper mold 4. The hemispherical curved cavity 3 communicates ...
PUM
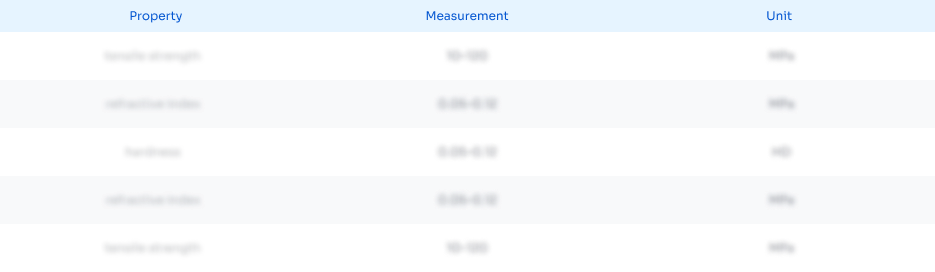
Abstract
Description
Claims
Application Information

- R&D
- Intellectual Property
- Life Sciences
- Materials
- Tech Scout
- Unparalleled Data Quality
- Higher Quality Content
- 60% Fewer Hallucinations
Browse by: Latest US Patents, China's latest patents, Technical Efficacy Thesaurus, Application Domain, Technology Topic, Popular Technical Reports.
© 2025 PatSnap. All rights reserved.Legal|Privacy policy|Modern Slavery Act Transparency Statement|Sitemap|About US| Contact US: help@patsnap.com