Main shaft apparatus
A spindle device and bearing technology, which is applied in the direction of large fixed members, metal processing machinery parts, maintenance and safety accessories, etc., can solve problems such as heat sticking, wear, and preload increase
- Summary
- Abstract
- Description
- Claims
- Application Information
AI Technical Summary
Problems solved by technology
Method used
Image
Examples
no. 1 approach )
[0193] like figure 1 As shown, the spindle device 10 has a built-in motor, and a hollow rotating shaft 12 is provided at the axial center thereof, and a slidable drawbar 13 is inserted into the shaft core of the rotating shaft 12 . The pull rod 13 exerts force on the collet portion 15 of the fixed tool holder 14 in the direction opposite to the tool (right direction in the figure) by the force of the disc spring 17, and the tool holder 14 fits into the conical surface 18 of the rotating shaft 12. . A tool (not shown) is attached to the tool holder 14 , and as a result, the tool can be attached to one end (left side in the figure) of the rotary shaft 12 so as to sandwich the tool.
[0194] In addition, the rotating shaft 12 is supported on the housing H by the two rows of front bearings 50, 50 supporting the tool side of the rotating shaft 12 and the two rows of rear bearings 60, 60 supporting the opposite side of the tool, so that it can be Free spins. It should be noted t...
no. 2 approach )
[0235] Next, refer to Figure 4 A spindle device according to a second embodiment of the present invention will be described in detail. In addition, the same code|symbol is attached|subjected to the same or equivalent part as 1st Embodiment, and the description is abbreviate|omitted or simplified.
[0236] In the second embodiment, in addition to the first cylindrical member 71 made of a metal material and the second cylindrical member 72 made of a carbon fiber composite material (CFRP) as in the first embodiment, the rotating shaft 12 also has Arranged on the outer peripheral surface of the second sleeve member 72, the inner rings 52, 52 of the front bearings 50, 50 and the inner rings 62, 62 of the rear bearings 60, 60 are respectively fitted on the outer peripheral surfaces. Two third cylindrical members 73,74.
[0237] The second cylindrical member 72 has stepped portions 72a, 72b at the front and rear portions of the outer peripheral surface away from the axially interm...
no. 3 approach )
[0261] Next, refer to Figure 7 , the spindle device according to the third embodiment of the present invention will be described in detail. In addition, the same code|symbol is attached|subjected to the same or equivalent part as 1st Embodiment, and the description is abbreviate|omitted or simplified.
[0262] In the third embodiment, the rotor 20 of the motor M is configured to be rotatable integrally with the rotary shaft 12 via the rotor sleeve 70 . In addition, the rotary shaft 12 is made of a metal material, and on the other hand, the rotor sleeve 70 is made of a carbon fiber composite material (CFRP). Carbon fiber composite materials (CFRP) use materials with lower heat transfer coefficient and thermal expansion coefficient than metal materials, higher specific elastic modulus and lower specific gravity than metal materials. In particular, by making the rotor sleeve 70 made of carbon fiber composite material with a small heat transfer coefficient and disposing it betw...
PUM
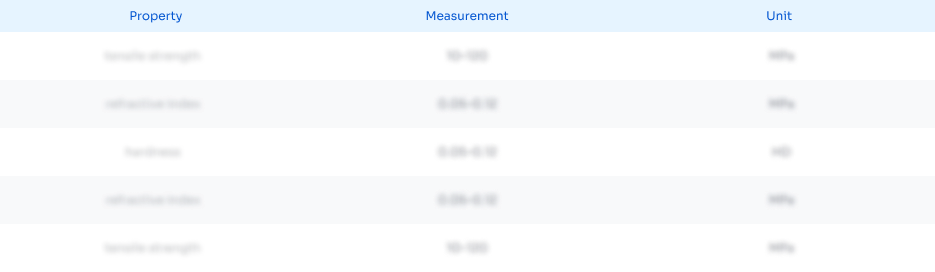
Abstract
Description
Claims
Application Information

- R&D
- Intellectual Property
- Life Sciences
- Materials
- Tech Scout
- Unparalleled Data Quality
- Higher Quality Content
- 60% Fewer Hallucinations
Browse by: Latest US Patents, China's latest patents, Technical Efficacy Thesaurus, Application Domain, Technology Topic, Popular Technical Reports.
© 2025 PatSnap. All rights reserved.Legal|Privacy policy|Modern Slavery Act Transparency Statement|Sitemap|About US| Contact US: help@patsnap.com