Pipe fitting with double galvanized layers and manufacturing method thereof
A manufacturing method and technology for pipe fittings, applied in the coating of superimposed layers, pipes/pipe joints/pipe fittings, coatings, etc., can solve the problems of thin coatings, impact resistance, corrosion resistance, etc., and can not meet the requirements, so as to achieve a bright color of the zinc layer Beautiful appearance, improved reputation and uniform zinc layer
- Summary
- Abstract
- Description
- Claims
- Application Information
AI Technical Summary
Problems solved by technology
Method used
Image
Examples
Embodiment 1
[0018] Embodiment 1, a pipe fitting with double coating, is characterized in that: the pipe fitting 1 made of malleable steel has a layer of hot-dip galvanized layer 2 on the inner and outer surfaces, and a layer of electro-galvanized layer 3 on the outside of the hot-dip galvanized layer, and the surface of the threaded part has only one layer Galvanized layer.
Embodiment 2
[0019] Embodiment 2, a method for manufacturing pipe fittings with double coatings, comprising the following steps: A. hot-dip galvanizing, including several processes of drying → galvanizing → galvanizing → cleaning → cooling, B. thread processing, C. electroplating Zinc, including the following steps: chemical degreasing or thermal degreasing → water washing → electrolytic degreasing → water washing → pickling → water washing → hydrochloric acid water washing → water washing → electrogalvanizing → water washing → hydrochloric acid water washing → water washing → passivation → water washing after passivation → passivation Second washing after melting→hot air drying→quality inspection.
[0020] The method of hot-dip galvanizing is as follows: a. For drying, the castings should be placed on the drying net to be turned and flattened at any time, so that the castings can be heated evenly and dried quickly; the baked castings should be preheated or loaded immediately Cage, b. Zinc...
PUM
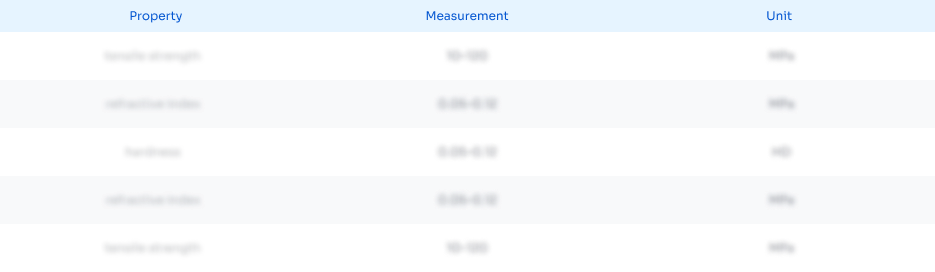
Abstract
Description
Claims
Application Information

- Generate Ideas
- Intellectual Property
- Life Sciences
- Materials
- Tech Scout
- Unparalleled Data Quality
- Higher Quality Content
- 60% Fewer Hallucinations
Browse by: Latest US Patents, China's latest patents, Technical Efficacy Thesaurus, Application Domain, Technology Topic, Popular Technical Reports.
© 2025 PatSnap. All rights reserved.Legal|Privacy policy|Modern Slavery Act Transparency Statement|Sitemap|About US| Contact US: help@patsnap.com