Method for heat application of low-alkalinity casting residue in steel-making
An application method and casting slag technology, applied in the field of metallurgy, can solve problems such as increased power consumption, aggravated smelting molten steel peroxidation, and insufficient heat, and achieves the effects of reducing treatment costs, reducing environmental pressure, and obvious environmental benefits
- Summary
- Abstract
- Description
- Claims
- Application Information
AI Technical Summary
Problems solved by technology
Method used
Image
Examples
Embodiment 1
[0031] 1. After tapping the steel in the upper furnace, add the high-basic hot final slag to 200kg magnesite balls for 3.5 minutes to splash the slag and leave it in the furnace (slag splash pressure 0.85MPa, slag splash gun position 800mm~1400mm), splash dry Finally, 1000kg of lime is added to the bottom of the converter before the semi-steel is put into the furnace, and then 350kg of hot cast slag with low alkalinity in the ladle is added to the converter for smelting along with 63t of the semi-steel (the carbon content of the semi-steel is 2.99%, and the phosphorus content is 0.377%).
[0032] Main Chemical Components of Low Basicity Casting Slag
[0033]
[0034] 2. When the gun blowing slag material starts to melt, start to add lime in small batches, 550Kg of lime is added in the early stage, and 300kg of lime is added after blowing for 3 minutes.
[0035] 3. Add 1000Kg of lime to 8 minutes of blowing, then add 400Kg of lime in 12 minutes, and turn down the furnace onc...
Embodiment 2
[0038] 1. After tapping the steel in the upper furnace, add the high-basic hot final slag to 200kg magnesite balls to splash the slag for 2.8 minutes and leave it in the furnace. After that, 1100kg of lime is added to the bottom of the converter before the semi-steel is put into the furnace, and then 320kg of hot casting slag with low alkalinity in the ladle is put into the converter for smelting along with 63.5t semi-steel (the carbon content of the semi-steel is 3.51%, and the phosphorus content is 0.462%).
[0039] 2. When the gun blowing slag material starts to melt, start to add lime in small batches, 650Kg of lime in the early stage, and 200kg of lime after blowing for 2.5 minutes.
[0040] 3. Add 1200Kg of lime to 8 minutes of blowing, and then add 300Kg of lime to 12 minutes. After blowing for 30 seconds to melt slag, turn down the furnace once.
[0041] 4. The temperature of the primary furnace is 1622°C, the carbon content is 0.09%, and the phosphorus content is 0.02...
Embodiment 3
[0044]1. After tapping the steel in the upper furnace, add high-basicity hot final slag to 200Kg magnesite balls to splash the slag for 3.2 minutes and leave it in the furnace. Finally, 1050kg of lime is added to the bottom of the converter before the semi-steel is put into the furnace, and then 390kg of hot casting slag with low alkalinity in the ladle is put into the converter for smelting along with 62.8t semi-steel (the carbon content of the semi-steel is 3.47%, and the phosphorus content is 0.618%).
[0045] 2. When the gun blowing slag material starts to melt, start to add lime in multiple batches, first add 570kg of lime, and then add 360kg of lime after blowing for 3 minutes.
[0046] 3. Add 1000kg of lime to 9 minutes of blowing, add 550kg of lime to 13 minutes, and turn down the furnace once every 35 seconds to 14 to differentiate slag.
[0047] 4. The temperature of the primary furnace is 1618°C, the carbon content is 0.11%, and the phosphorus content is 0.034%.
...
PUM
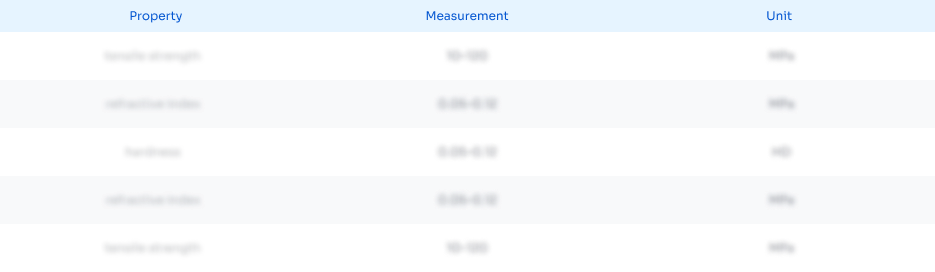
Abstract
Description
Claims
Application Information

- R&D
- Intellectual Property
- Life Sciences
- Materials
- Tech Scout
- Unparalleled Data Quality
- Higher Quality Content
- 60% Fewer Hallucinations
Browse by: Latest US Patents, China's latest patents, Technical Efficacy Thesaurus, Application Domain, Technology Topic, Popular Technical Reports.
© 2025 PatSnap. All rights reserved.Legal|Privacy policy|Modern Slavery Act Transparency Statement|Sitemap|About US| Contact US: help@patsnap.com