Method for manufacturing rim of inner tire-free wheel
A manufacturing method and rim technology, which can be used in manufacturing tools, auxiliary devices, auxiliary welding equipment, etc., can solve the problems of rim welding dislocation and reduce grinding workload.
- Summary
- Abstract
- Description
- Claims
- Application Information
AI Technical Summary
Problems solved by technology
Method used
Image
Examples
Embodiment Construction
[0016] Below in conjunction with accompanying drawing, this patent is described in further detail.
[0017] Such as figure 1 Shown, the manufacturing method of tubeless wheel rim of the present invention comprises the steps:
[0018] (1) Cut the prefabricated rim profile according to the diameter of the rim and roll it into a circle;
[0019] (2) The rounded rim profiles are rounded in turn, then cut and rounded;
[0020] (3) Heating both ends of the rounded wheel rim profile obtained in step (2) at 350°C-450°C and then pressing it to form a uniform arc of the welding part of the rim;
[0021] (4) butt-weld the rim profiles obtained in step (3) with the same curvature of the welding part to obtain the rim blank;
[0022] (5), scraping slag on the rim preliminary blank after butt welding obtained in step (4);
[0023] (6) Carry out rolling after heating the weld seam after scraping the slag, the heating temperature is 350°C-450°C.
[0024] In practical application, the tem...
PUM
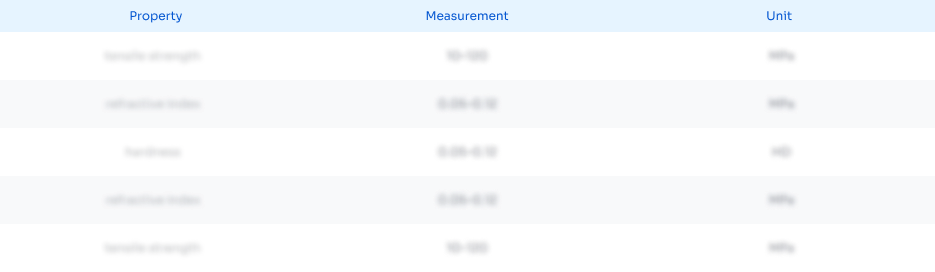
Abstract
Description
Claims
Application Information

- R&D Engineer
- R&D Manager
- IP Professional
- Industry Leading Data Capabilities
- Powerful AI technology
- Patent DNA Extraction
Browse by: Latest US Patents, China's latest patents, Technical Efficacy Thesaurus, Application Domain, Technology Topic, Popular Technical Reports.
© 2024 PatSnap. All rights reserved.Legal|Privacy policy|Modern Slavery Act Transparency Statement|Sitemap|About US| Contact US: help@patsnap.com