Method for preparing 4A molecular sieve from bauxite tailings
A technology of bauxite and molecular sieve, applied in the direction of crystalline aluminosilicate zeolite, A-type crystalline aluminosilicate zeolite, etc.
- Summary
- Abstract
- Description
- Claims
- Application Information
AI Technical Summary
Problems solved by technology
Method used
Image
Examples
Embodiment 1
[0027] The raw material of the present invention is the bauxite tailings in Henan, the chemical composition of the bauxite tailings is as shown in Table 1, and the other is mainly crystal water and volatile matter, and trace elements such as Ca, S, Mg, Zr, Cr, Mn et al.
[0028]
[0029] Table 1: Chemical composition of bauxite tailings (%wt)
[0030] al 2 o 3 SiO 2 Fe 2 o 3 TiO 2 K 2 o other Bauxite tailings 51.00 26.70 13.28 3.30 3.25 2.47
[0031] Its synthetic steps are:
[0032] (1) Iron removal by acid method: take 30g of bauxite tailings less than 10μm and grind it with 500mL of 3mol / L hydrochloric acid to react at 100°C for 2 hours to remove iron. and dry.
[0033] (2) Mine-soda co-melting: Put the above-mentioned iron-removed tailings and solid NaOH in a graphite crucible to react in a muffle furnace, where the ratio of ore-soda is 1:1.5, heat to 500°C for calcination and hold for 30 minutes. The calcined product is ...
Embodiment 2
[0039] Experiment raw material is with embodiment 1
[0040] The synthesis steps are:
[0041] (1) Iron removal by acid method: take 30g of bauxite tailings less than 10μm and grind it with 500mL of 3mol / L hydrochloric acid to react at 100°C for 2 hours to remove iron. and dry.
[0042] (2) Mine-soda eutectic: Put the above-mentioned iron-removed tailings and solid NaOH in a graphite crucible to react in a muffle furnace, where the ratio of ore-soda is 1:1, heat to 500°C for calcination and hold for 60 minutes. The calcined product is ground to a fineness below 30 μm.
[0043] (3) Deployment solution: Take 8g of ore alkali eutectic product and dissolve it in 400mLH 2 O, stirred at room temperature for 1 h, filtered to separate the insoluble matter, and took the supernatant. Add 9g of sodium silicate nonahydrate to the clear liquid, fully dissolve and stir at 65°C for 2h.
[0044] (4) Crystallization reaction: the silicon-aluminum solution described in step (3) is placed i...
Embodiment 3
[0047] Experiment raw material is with embodiment 1
[0048] The synthesis steps are:
[0049] (1) Iron removal by acid method: take 30g of bauxite tailings less than 10μm and grind it with 500mL of 3mol / L hydrochloric acid to react at 100°C for 2 hours to remove iron. and dry.
[0050] (2) Mineral alkali co-melting: Put the above iron-removed tailings and solid NaOH in a graphite crucible to react in a muffle furnace, where the ratio of mineral to alkali is 1:1.5, heat to 600°C for calcination and hold for 30 minutes. The calcined product is ground to a fineness below 30 μm.
[0051] (3) Deployment solution: Take 8g of ore alkali eutectic product and dissolve it in 400mLH 2 O, stirred at room temperature for 1 h, filtered to separate the insoluble matter, and took the supernatant. Add 7g of sodium silicate nonahydrate to the clear liquid, fully dissolve and stir at 65°C for 2h.
[0052] (4) Crystallization reaction: the silicon-aluminum solution described in step (3) is ...
PUM
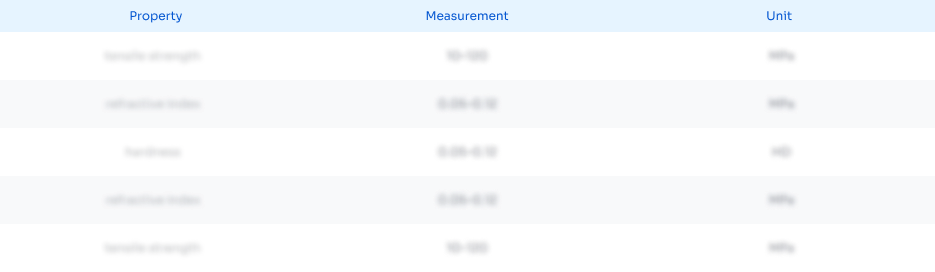
Abstract
Description
Claims
Application Information

- Generate Ideas
- Intellectual Property
- Life Sciences
- Materials
- Tech Scout
- Unparalleled Data Quality
- Higher Quality Content
- 60% Fewer Hallucinations
Browse by: Latest US Patents, China's latest patents, Technical Efficacy Thesaurus, Application Domain, Technology Topic, Popular Technical Reports.
© 2025 PatSnap. All rights reserved.Legal|Privacy policy|Modern Slavery Act Transparency Statement|Sitemap|About US| Contact US: help@patsnap.com