Asymmetrical stainless steel filter membrane tube and production method thereof
A stainless steel, asymmetric technology, used in chemical instruments and methods, layered products, metal layered products, etc., can solve the problems of low strength, complex methods, short product life, etc., to improve the sintering yield and improve the permeability coefficient, the effect of ensuring the filtering accuracy
- Summary
- Abstract
- Description
- Claims
- Application Information
AI Technical Summary
Problems solved by technology
Method used
Image
Examples
Embodiment 1
[0026] The stainless steel fiber felt that filter precision is 20um is packed in the groove 7 that comprises charging port 1, charging port 2 and the molding die of mandrel (see image 3 ), after the mandrel and the rubber sleeve are fixed, load -180~300 mesh stainless steel powder into the charging port 1, and at the same time load the -300 mesh stainless steel powder into the charging port 2. During the charging process, it must be ensured The powder height of coarse powder and fine powder in the mold is alternately increased in order to ensure the uniformity of the thickness of different powder gradient layers. Put the loaded powder together with the mold into the cold isostatic press for compression molding, and then take it out for demoulding ; This asymmetric stainless steel filter membrane tube green body is sintered in a vacuum furnace at a sintering temperature of 1200 ° C. During sintering, the temperature is raised at a low speed at a specific temperature to prevent ...
Embodiment 2
[0028] The stainless steel fiber felt that filter precision is 20um is packed in the groove 7 of mould, see image 3 , after the mandrel and the rubber sleeve are fixed, load -180~340 mesh stainless steel powder into the charging port 1, and at the same time load the -340 mesh stainless steel powder into the charging port 2, and the coarseness must be ensured during the charging process. The powder height of powder and fine powder in the mold increases alternately in order to ensure the uniformity of different powder gradient layers. Put the loaded powder together with the mold into a cold isostatic press for pressing and molding, and then take it out for demoulding; sinter the asymmetric stainless steel filter membrane tube green body in a vacuum furnace at a sintering temperature of 1150°C. A low-speed heating is carried out at a specific temperature to prevent the sample from cracking; finally, an asymmetric stainless steel filter membrane tube is obtained.
Embodiment 3
[0030] The stainless steel fiber felt that filter precision is 20um is packed in the groove 7 of mould, see image 3 , after the mandrel and the rubber sleeve are fixed, load -300 mesh stainless steel powder into the charging port 1, and at the same time load -180 ~ 300 mesh stainless steel powder into the charging port 2. During the charging process, it is necessary to ensure that the coarse The powder height of powder and fine powder in the mold increases alternately in order to ensure the uniformity of different powder gradient layers. Put the loaded powder together with the mold into the isostatic press to form it, and then take it out for demoulding; the asymmetric stainless steel filter membrane tube green body is sintered in the hydrogen atmosphere of the hydrogen furnace, the sintering temperature is 1200°C, and the A low-speed heating is carried out at a specific temperature to prevent the sample from cracking; finally, an asymmetric stainless steel filter membrane tu...
PUM
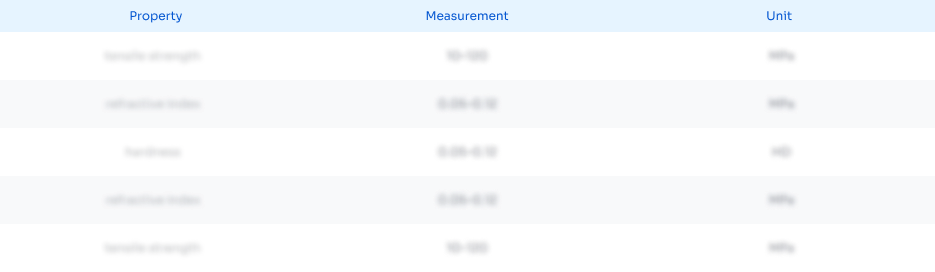
Abstract
Description
Claims
Application Information

- R&D Engineer
- R&D Manager
- IP Professional
- Industry Leading Data Capabilities
- Powerful AI technology
- Patent DNA Extraction
Browse by: Latest US Patents, China's latest patents, Technical Efficacy Thesaurus, Application Domain, Technology Topic, Popular Technical Reports.
© 2024 PatSnap. All rights reserved.Legal|Privacy policy|Modern Slavery Act Transparency Statement|Sitemap|About US| Contact US: help@patsnap.com