Denitration catalyst of wide activity temperature window as well as preparation method and application thereof
A technology of active temperature window and denitrification catalyst, which is applied in the direction of chemical instruments and methods, physical/chemical process catalysts, separation methods, etc., can solve the flue gas conditions and precursors of catalysts with low denitrification performance and cannot be applied to low-load operation of power plant boilers High toxicity and other problems, to achieve the effect of widening the active temperature window and improving low-temperature denitrification performance
- Summary
- Abstract
- Description
- Claims
- Application Information
AI Technical Summary
Problems solved by technology
Method used
Image
Examples
Embodiment 1
[0017] Example 1: Cu 0.1 Ce 0.1 Ti 0.8 o 2 Preparation of composite oxide catalyst
[0018] a) Take 7.53 ml of 0.50 mol / L copper nitrate solution, 7.49 ml of 0.50 mol / L cerium nitrate solution and 15.03 ml of 2 mol / L titanium sulfate solution, stir and mix in a water bath at 30°C for 30 minutes to obtain a mixed solution;
[0019] b) Add ammonia water to the mixed solution obtained in step a) under constant stirring until the pH value is 10, transfer the obtained mixed solution to a hydrothermal reaction kettle, perform a hydrothermal reaction at 120° C. for 24 hours, and then lower it to room temperature;
[0020] c) The reaction solution obtained in step b) was suction-filtered, washed, dried at 120°C for 12 hours, and then calcined in a muffle furnace at 500°C for 6 hours to prepare a copper-cerium-titanium composite oxide catalyst.
Embodiment 2
[0021] Example 2: Cu 0.1 Ce 0.3 Ti 0.6 o 2 Preparation of composite oxide catalyst
[0022] a) Take 3.77 ml of 1.0 mol / L copper nitrate solution, 11.31 ml of 1.0 mol / L cerium nitrate solution and 22.62 ml of 1.0 mol / L titanium sulfate solution, stir and mix in a water bath at 50°C for 90 minutes to obtain a mixed solution;
[0023] b) adding ammonia water to the mixed solution obtained in step a) under constant stirring until the pH value is 10, transferring the obtained mixed solution to a hydrothermal reaction kettle, performing a hydrothermal reaction at 120° C. for 12 hours, and then cooling down to room temperature;
[0024] c) The reaction solution obtained in step b) was suction filtered, washed, dried at 120°C for 24 hours, and then calcined in a muffle furnace at 500°C for 4 hours to prepare a copper-cerium-titanium composite oxide catalyst.
Embodiment 3
[0025] Example 3: Cu 0.2 Ce 0.2 Ti 0.6 o 2 Preparation of composite oxide catalyst
[0026] a) Take 7.53 ml of 1.0 mol / L copper nitrate solution, 7.49 ml of 1.0 mol / L cerium nitrate solution and 11.27 ml of 2 mol / L titanium sulfate solution, stir and mix in a water bath at 30°C for 60 minutes to obtain a mixed solution;
[0027] b) Add ammonia water to the mixed solution obtained in step a) under constant stirring until the pH value is 10, transfer the obtained mixed solution to a hydrothermal reaction kettle, perform a hydrothermal reaction at 120° C. for 24 hours, and then lower it to room temperature;
[0028] c) The reaction solution obtained in step b) was suction-filtered, washed, dried at 120°C for 48 hours, and then calcined in a muffle furnace at 500°C for 8 hours to prepare a copper-cerium-titanium composite oxide catalyst.
PUM
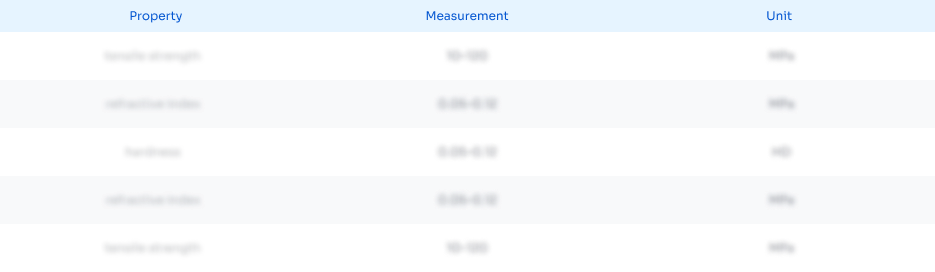
Abstract
Description
Claims
Application Information

- R&D
- Intellectual Property
- Life Sciences
- Materials
- Tech Scout
- Unparalleled Data Quality
- Higher Quality Content
- 60% Fewer Hallucinations
Browse by: Latest US Patents, China's latest patents, Technical Efficacy Thesaurus, Application Domain, Technology Topic, Popular Technical Reports.
© 2025 PatSnap. All rights reserved.Legal|Privacy policy|Modern Slavery Act Transparency Statement|Sitemap|About US| Contact US: help@patsnap.com