Catalyst for preparing 4, 4'-diaminodiphenyl ether, preparation method and application of catalyst
A technology of diaminodiphenyl ether and dinitrodiphenyl ether, applied in the field of fine organic product synthesis, can solve the problems of high cost, easy carbon deposition, environmental pollution, etc., and achieve industrial batch production, high conversion rate and production efficiency rate effect
- Summary
- Abstract
- Description
- Claims
- Application Information
AI Technical Summary
Problems solved by technology
Method used
Examples
Embodiment 1
[0019] 1. Preparation of catalyst: 12.3g of Ni(NO 3 ) 2 ·6H 2 O and 4.7g of Cu(NO 3 ) 2 ·3H 2 O is completely dissolved in a certain amount of deionized water to form a mixed aqueous solution of nitrate, and then 21.3g of -Al 2 o 3 Pour into the prepared nitrate mixed aqueous solution to form equal volume impregnation. The mixture was dried in an oven at 100°C for 12 hours, then calcined at 350°C for 3 hours under a nitrogen atmosphere, and finally heated in H 2 -N 2 (H 2 and N 2 The molar ratio is 3:7) and reduced at 300°C for 1 hour in a mixed atmosphere to obtain Ni-Cu / -Al 2 o 3 Catalyst, wherein weight percent is Ni: 10%, Cu: 5%, -Al 2 o 3 : 85%.
[0020] 2. Production of 4,4'-diaminodiphenyl ether: Add 250mL of 1,2-dichloroethane as a reaction solvent into a 500mL autoclave, and then add 100g of raw material 4,4'-dinitrodiphenyl Phenyl ether and 1g of the above-mentioned catalyst were added to the kettle, and the autoclave was purged with nitrogen fo...
Embodiment 2
[0022] 1. Preparation of catalyst: 18.5g of Ni(NO 3 ) 2 ·6H 2 O and 21.4g of Mg(NO 3 ) 2 ·6H 2 O is completely dissolved in a certain amount of deionized water to form a mixed aqueous solution of nitrate, and then 19.3g of -Al 2 o 3 Pour into the prepared nitrate mixed aqueous solution to form equal volume impregnation. The mixture was dried in an oven at 110°C for 15 hours, then calcined at 450°C for 4 hours under a nitrogen atmosphere, and finally heated in H 2 -N 2 (H 2 and N 2 The molar ratio is 3:7) and reduced at 400°C for 2 hours in a mixed atmosphere to obtain Ni-Mg / -Al 2 o 3 Catalyst, wherein weight percent is 15% Ni, 8% Mg and 77% -Al 2 o 3 .
[0023] 2. Production of 4,4'-diaminodiphenyl ether: Add 250mL of 1,2-dichloroethane as a reaction solvent into a 500mL autoclave, and then add 100g of raw material 4,4'-dinitrodiphenyl Phenyl ether and 1.5g of the above-mentioned catalyst were added to the autoclave, and the autoclave was purged with nitr...
Embodiment 3
[0025] 1. Preparation of catalyst: 24.7g of Ni(NO 3 ) 2 ·6H 2 O and 19.2g of Cr(NO 3 ) 3 9H 2 O was completely dissolved in a certain amount of deionized water to form a nitrate mixed aqueous solution, and then 17.5 g of activated carbon was poured into the prepared nitrate mixed aqueous solution to form an equal-volume impregnation. The mixture was dried in an oven at 120°C for 24 hours, then calcined at 500°C for 5 hours under a nitrogen atmosphere, and finally heated in H 2 -N 2 (H 2 and N 2 The molar ratio is 3:7) and reduced at 450°C for 3 hours in a mixed atmosphere to obtain a Ni-Cr / activated carbon catalyst, in which the weight percentage is 20% Ni, 10% Cr and 70% activated carbon.
[0026] 2. Production of 4,4'-diaminodiphenyl ether: Add 250mL of 1,2-dichloroethane as a reaction solvent into a 500mL autoclave, and then add 100g of raw material 4,4'-dinitrodiphenyl Phenyl ether and 2.0g of the above catalyst were added to the kettle, and the autoclave was purg...
PUM
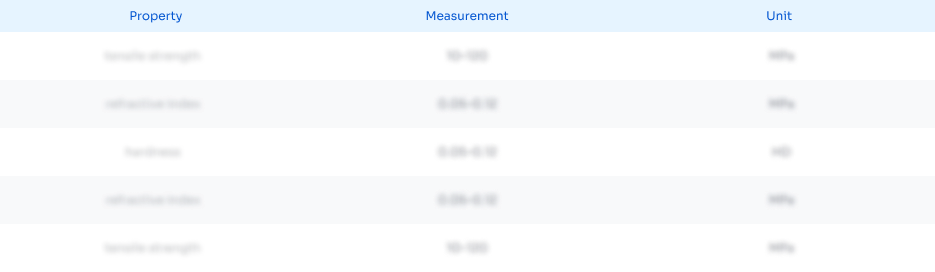
Abstract
Description
Claims
Application Information

- R&D Engineer
- R&D Manager
- IP Professional
- Industry Leading Data Capabilities
- Powerful AI technology
- Patent DNA Extraction
Browse by: Latest US Patents, China's latest patents, Technical Efficacy Thesaurus, Application Domain, Technology Topic, Popular Technical Reports.
© 2024 PatSnap. All rights reserved.Legal|Privacy policy|Modern Slavery Act Transparency Statement|Sitemap|About US| Contact US: help@patsnap.com