Preparation method of 180 grade polyurethane enamelled wire insulating paint used for ultra-fine wire
A technology of polyurethane paint and insulating paint, applied in the direction of polyurea/polyurethane coatings, coatings, etc., can solve the problems of poor resistance to salt water pinholes and poor leveling of paint liquid, and achieve good resistance to saltwater pinholes, Good direct weldability and smooth surface
- Summary
- Abstract
- Description
- Claims
- Application Information
AI Technical Summary
Problems solved by technology
Method used
Examples
Embodiment 1
[0019] Synthesize polyester resin according to the method of the present invention, for synthesizing the polyester resin of imine five-membered ring modification, make through the following steps: first drop into ethylene glycol, glycerol and the acetic acid that accounts for total charging amount 0.01% in reaction kettle Zinc, stir to raise the temperature of the kettle to 60°C, put in TMP and DMT, gradually raise the temperature to 225°C, collect fractions, cool down to 165°C when there are no fractions, put in trimellitic anhydride and 4,4'-diaminodiphenylmethane, and heat up to 200°C , when there is no distillate, cool down to 70°C, add m-cresol and xylene to dilute the polyester resin with a solid content of 44%, cool down to 50°C for later use. The molar ratio of imine five-membered ring to DMT is 1:1.2.
[0020] Synthesize blocked isocyanate according to the method of the present invention, according to the following steps: first drop into described polyester resin, tri...
Embodiment 2
[0023] Synthesize modified polyester resin according to the method in Example 1, wherein the molar ratio of imine five-membered ring to DMT is 1:1.2; synthesize blocked isocyanate according to the method in Example 1; let down the paint according to the method in Example 1, and control the amino condensate The addition ratio of the silicone oil is 0.35 parts, the silicone oil ratio is 0.04 parts, and the acrylate is 0.6 parts. 180-grade polyurethane enameled wire insulating varnish is used to generate ultra-fine wires, with a solid content of 22%, a viscosity of 15-17 seconds at 30°C, and apply 4 cups.
Embodiment 3
[0025] Synthesize polyester resin according to the method of Example 1, wherein the molar ratio of imine five-membered ring to DMT is 1:1.1; synthesize blocked isocyanate according to the method of Example 1; let down the paint according to the method of the present invention, and control the addition ratio of amino condensate 0.75 parts, silicone oil ratio is 0.03 parts, acrylate is 0.6 parts. 180-grade polyurethane enameled wire insulating varnish is used to generate ultra-fine wires, with a solid content of 22%, a viscosity of 15-17 seconds at 30°C, and apply 4 cups.
PUM
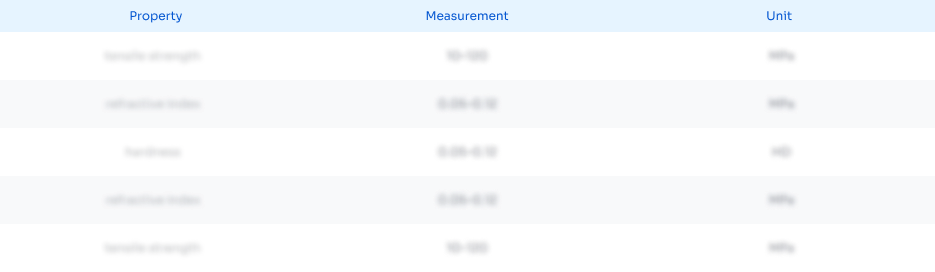
Abstract
Description
Claims
Application Information

- Generate Ideas
- Intellectual Property
- Life Sciences
- Materials
- Tech Scout
- Unparalleled Data Quality
- Higher Quality Content
- 60% Fewer Hallucinations
Browse by: Latest US Patents, China's latest patents, Technical Efficacy Thesaurus, Application Domain, Technology Topic, Popular Technical Reports.
© 2025 PatSnap. All rights reserved.Legal|Privacy policy|Modern Slavery Act Transparency Statement|Sitemap|About US| Contact US: help@patsnap.com