Isothermal thermoforming hydraulic press
A warm forming and hydraulic press technology, applied in the field of hydraulic machinery, can solve the problems of increased forging difficulty, waste of energy, large heat loss, etc., and achieve the effects of improving the overall rigidity, compacting the overall structure, and reducing the span
- Summary
- Abstract
- Description
- Claims
- Application Information
AI Technical Summary
Problems solved by technology
Method used
Image
Examples
Embodiment Construction
[0021] In order to further understand the invention content, characteristics and effects of the present invention, the following examples are given, and detailed descriptions are as follows in conjunction with the accompanying drawings:
[0022] see Figure 1-Figure 4 , isothermal thermoforming hydraulic press, including three-beam four-column fuselage composed of upper beam 1, lower beam 2 and column 3 fastened by lock nut 11, working oil cylinder 6 installed on the upper beam, and slider connected with the working oil cylinder 4 and the workbench arranged on the lower beam. A guide column 7 for guiding the slider is mounted on the upper beam, and a guide sleeve 8 is provided between the upper beam and the guide column. In this embodiment, the guide sleeve between the upper beam and the guide column is Wear-resistant guide bush made of composite material. A heat-resistant ceramic plate 12 is fixedly mounted on the periphery of the lower plane of the slider. The workbench i...
PUM
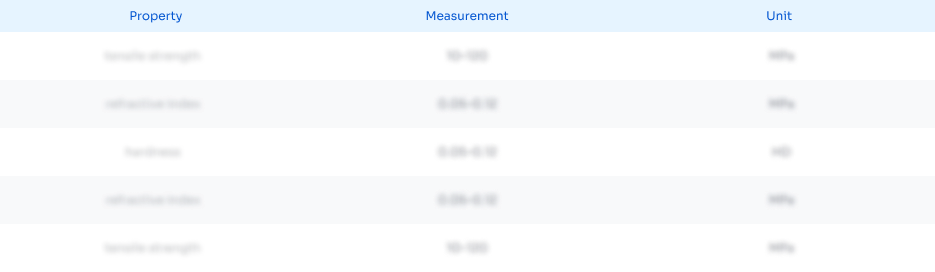
Abstract
Description
Claims
Application Information

- R&D
- Intellectual Property
- Life Sciences
- Materials
- Tech Scout
- Unparalleled Data Quality
- Higher Quality Content
- 60% Fewer Hallucinations
Browse by: Latest US Patents, China's latest patents, Technical Efficacy Thesaurus, Application Domain, Technology Topic, Popular Technical Reports.
© 2025 PatSnap. All rights reserved.Legal|Privacy policy|Modern Slavery Act Transparency Statement|Sitemap|About US| Contact US: help@patsnap.com