Method for improving filtering efficiency of tobacco powder extracting solution during production of tobacco sheets through paper-making process
A technology of tobacco sheet, production process, applied in the direction of tobacco, preparation of tobacco, application, etc.
- Summary
- Abstract
- Description
- Claims
- Application Information
AI Technical Summary
Problems solved by technology
Method used
Image
Examples
Embodiment 1
[0030] Add cationic guar gum with a molecular weight of 500,000 slowly into water under stirring conditions, dilute to 1% by mass, stir thoroughly for 30 minutes, then heat the solution to 40°C, keep stirring for 90 minutes and then stir for later use.
[0031] Dilute the dissolved cationic guar gum to 0.1% (mass percentage), stir well, and then add it to the tobacco powder extract to be filtered, the addition amount is 0.4% (relative to the dry mass ratio of tobacco powder), at 500 rpm / min speed stirring for 3 minutes, and then sent to the filter for dehydration.
[0032] Compared with the control group without cationic guar gum, the unit filtration time was shortened by 40%, and the filtration efficiency was significantly improved. The average number of equipment unpacking and washing in the control group without adding cationic guar gum was 21 times / month. After filtering with cationic guar gum in this example, the average number of equipment dismantling and washing was 1...
Embodiment 2
[0034] First add cationic guar gum with a molecular weight of 500,000 to water slowly under stirring conditions, dilute to 1% by mass, stir thoroughly for 30 minutes, then heat the solution to 40°C, keep stirring for 90 minutes and then stir for later use .
[0035] The dissolved cationic guar gum is diluted to 0.1% (mass percentage), and fully stirred, and the diluted cationic guar gum is added from the pipeline through a metering pump in an amount of 0.3% relative to the absolute dry mass ratio of the tobacco powder. The pipe is the pipe located after the slurry pump of the smoke extraction equipment and before entering the filter.
[0036] Compared with the control group without the addition of cationic guar gum, the filtration efficiency was improved, because the equipment dismantling and cleaning time caused by the clogging of the filter screen was reduced by 41%.
Embodiment 3
[0038] First, add cationic guar gum with a molecular weight of 350,000 to water slowly under stirring conditions, dilute to 1% by mass, stir thoroughly for 20 minutes, then heat the solution to 30°C, keep stirring for 60 minutes, and then stir for later use .
[0039] Dilute the dissolved cationic guar gum to 0.1% (mass percentage), stir well, and then add it to the tobacco powder extract to be filtered, the addition amount is 0.5% (relative to the absolute dry mass ratio of the tobacco powder), at 600 rpm / min speed stirring for 2 minutes, and then sent to the filter for dehydration.
[0040] Compared with the control group without the addition of cationic guar gum, the filtration efficiency was improved, because the equipment disassembly and cleaning time due to filter blockage was reduced by 31%.
PUM
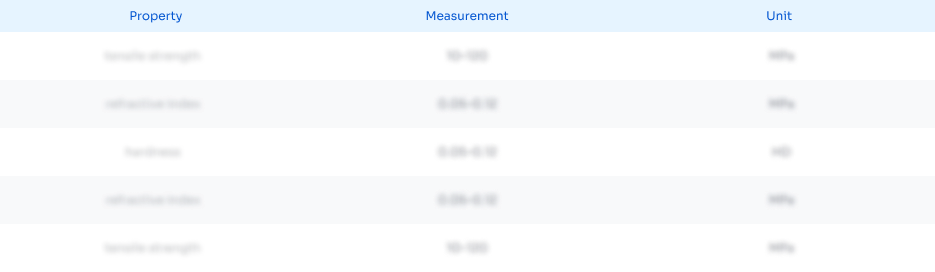
Abstract
Description
Claims
Application Information

- R&D Engineer
- R&D Manager
- IP Professional
- Industry Leading Data Capabilities
- Powerful AI technology
- Patent DNA Extraction
Browse by: Latest US Patents, China's latest patents, Technical Efficacy Thesaurus, Application Domain, Technology Topic, Popular Technical Reports.
© 2024 PatSnap. All rights reserved.Legal|Privacy policy|Modern Slavery Act Transparency Statement|Sitemap|About US| Contact US: help@patsnap.com