Recovery, balance adjustment and comprehensive utilization technology for mixing alkali in indigo blue production
A technology of balance adjustment and mixed alkali, applied in indigo dyes, organic dyes, chemical instruments and methods, etc., can solve the problems of underutilization of potassium resources, waste of resources, etc., and achieve a small investment, low investment and huge benefits. Effect
- Summary
- Abstract
- Description
- Claims
- Application Information
AI Technical Summary
Problems solved by technology
Method used
Examples
Embodiment 1
[0021] Example 1 Crystallization experiment at 70°C
[0022] Weigh 200.00 g of the three-effect concentrated solution (mixed alkali) (K / Na=0.62:1, CO 3 2- =15.54g / L, alkalinity (mixed alkali)=692.41g / L), pass into 15.00g CO in the mixed alkali 2 , immediately with white Na 2 CO 3 generated, and exothermic significantly, with the CO 2 The continuous feeding, the crystallization increases, when the reaction to CO 2 After feeding the specified amount, the reaction temperature reached about 62°C, and the CO 2 Introduce, keep warm at 70°C, continue to stir for 2 hours, after fully crystallizing and cooling, heat filter to obtain 154.00g of mother liquor (K / Na=1.08, CO 3 2- =41.45g / L, alkalinity (mixed alkali)=446.99g / L, potassium ion content 3.82%) and crude product Na 2 CO 3 38.79g (K / Na=0, CO 3 2- =51.03g / L, alkalinity (mixed alkali) =7.53%).
Embodiment 2
[0023] Example 2 Crystallization experiment at room temperature (20°C)
[0024] Weigh 200.00 g of the three-effect concentrated solution (K / Na=0.62:1, CO 3 2- =15.54g / L, alkalinity (mixed alkali)=692.41g / L), pass into 15.00g CO in the mixed alkali 2 , immediately with white Na 2 CO 3 generated, and exothermic significantly, with the CO 2 The continuous feeding, the crystallization increases, when the reaction to CO 2 After feeding the specified amount, the reaction temperature reached about 62°C, and the CO2 , cooled to room temperature, stirred for 2 hours to fully crystallize, filtered to obtain 155.00g of mother liquor (K / Na=1.08:1, CO 3 2- =41.93g / L, alkalinity (mixed alkali)=442.59g / L, potassium ion content 3.82%) and crude product Na 2 CO 3 36.40g (K / Na=0, CO 3 2- =51.63g / L, alkalinity (mixed alkali)=6.51%).
Embodiment 3
[0025] Example 3 Crystallization experiment at room temperature (0°C)
[0026] Weigh 200.00 g of the three-effect concentrated solution (K / Na=0.62:1, CO 3 2- =15.54g / L, alkalinity (mixed alkali)=692.41g / L), pass into 15.00g CO in the mixed alkali 2 , immediately with white Na 2 CO 3 generated, and exothermic significantly, with the CO 2 The continuous feeding, the crystallization increases, when the reaction to CO 2 After feeding the specified amount, the reaction temperature reached about 62°C, and the CO 2 , put it in ice water to cool, stir for 2 hours to fully crystallize, filter to obtain 154.00g of mother liquor (K / Na=1.08:1, CO 3 2- =43.22g / L, alkalinity (mixed alkali)=444.76g / L, potassium ion content 3.81%) and crude product Na 2 CO 3 35.40g (K / Na=0, CO 3 2- =50.76g / L, alkalinity (mixed alkali) =49.50%).
[0027] Implementation column 4
[0028] Weigh 200.00 g of the three-effect concentrated solution (K / Na=0.62:1, CO 3 2- =15.54g / L, alkalinity (mixed a...
PUM
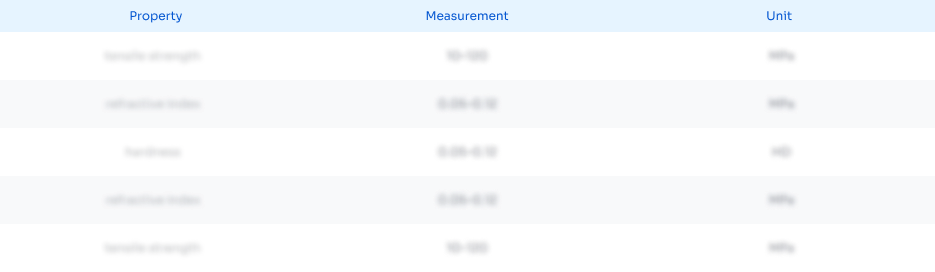
Abstract
Description
Claims
Application Information

- R&D Engineer
- R&D Manager
- IP Professional
- Industry Leading Data Capabilities
- Powerful AI technology
- Patent DNA Extraction
Browse by: Latest US Patents, China's latest patents, Technical Efficacy Thesaurus, Application Domain, Technology Topic, Popular Technical Reports.
© 2024 PatSnap. All rights reserved.Legal|Privacy policy|Modern Slavery Act Transparency Statement|Sitemap|About US| Contact US: help@patsnap.com