Preparation method for dialkyl phosphinates
A technology of dialkyl phosphinate and dialkyl phosphinic acid, which is applied in the field of preparation of dialkyl phosphinate, can solve the problem of unwanted telomer formation, decreased product yield, low product purity, etc. problems, to avoid the reduction of yield and purity, avoid the formation of telomers, and reduce the effect of reaction temperature
- Summary
- Abstract
- Description
- Claims
- Application Information
AI Technical Summary
Problems solved by technology
Method used
Image
Examples
Embodiment 1
[0031] Dissolve 300g of sodium hypophosphite monohydrate and 12g of sodium bisulfite in 1500g of water, then add it to the autoclave, replace it with nitrogen three times, start stirring, raise the temperature to 100°C, pass ethylene into the reactor, pass through the pressure reducing valve The pressure in the control kettle is about 0.6MPa. Dissolve 10g of 2,2'-azobis(2-amidinopropane) dihydrochloride in 100g of water, and continuously and evenly add it to the reactor within 6 hours. After the addition, the reaction was carried out at constant temperature and pressure for 1 hour to obtain sodium dialkylphosphinate.
[0032] Transfer the mixed solution of sodium dialkylphosphinate obtained above into a reactor equipped with a thermometer, stirring, condensing reflux pipe and dripping device, heat to 100°C, and then dissolve 350g of hexadecanohydrate sulfuric acid in 600g of water Aluminum was evenly added through the dropping funnel within 2 hours, refluxed for about 2 hours...
Embodiment 2
[0035] Dissolve 300g of sodium hypophosphite monohydrate and 20g of potassium bisulfite in 1000g of water, then add it to the autoclave, replace it with nitrogen three times, start stirring, raise the temperature to 120°C, pass ethylene into the reactor, pass through the pressure reducing valve The pressure in the control kettle is about 0.8MPa. Dissolve 12g of dibenzoyl peroxide in 100g of water, and continuously and evenly add it to the reaction kettle within 5 hours. After the addition, the reaction was carried out at constant temperature and pressure for 1 hour to obtain sodium dialkylphosphinate.
[0036] Transfer the mixed solution of sodium dialkylphosphinate obtained above into a reactor equipped with a thermometer, stirring, condensing reflux tube and dripping device, heat to 90°C, and then dissolve 350g of hexadecanohydrate sulfuric acid in 600g of water Aluminum was evenly added through the dropping funnel within 2 hours, refluxed for about 2 hours, cooled and filt...
Embodiment 3
[0040]Dissolve 350g of sodium hypophosphite monohydrate and 18g of sodium sulfite in 1000g of water, then add it to the autoclave, replace it with nitrogen three times, start stirring, raise the temperature to 120°C, feed ethylene into the reactor, and control the pressure inside the autoclave through a pressure reducing valve. The pressure is about 0.7MPa. Dissolve 12g of potassium persulfate in 100g of water, and continuously and evenly add to the reaction kettle within 5 hours. After the addition, the reaction was carried out at constant temperature and pressure for 1 hour to obtain sodium dialkylphosphinate.
[0041] Transfer the mixed solution of sodium dialkylphosphinate obtained above into a reactor equipped with a thermometer, stirring, condensing reflux pipe and dripping device, heat to 100°C, and then dissolve 420g of hexadecanohydrate sulfuric acid in 700g of water Aluminum was evenly added through the dropping funnel within 2 hours, refluxed for about 2 hours, coo...
PUM
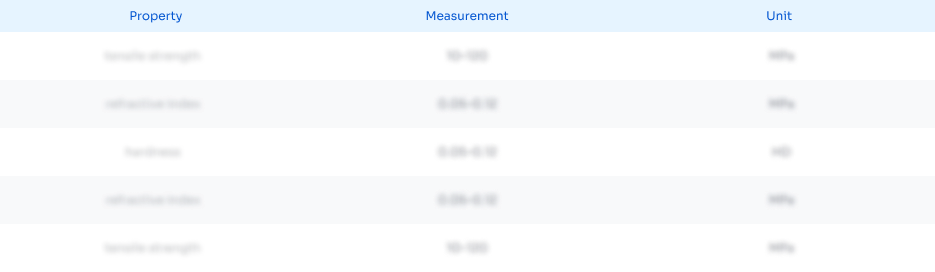
Abstract
Description
Claims
Application Information

- R&D Engineer
- R&D Manager
- IP Professional
- Industry Leading Data Capabilities
- Powerful AI technology
- Patent DNA Extraction
Browse by: Latest US Patents, China's latest patents, Technical Efficacy Thesaurus, Application Domain, Technology Topic, Popular Technical Reports.
© 2024 PatSnap. All rights reserved.Legal|Privacy policy|Modern Slavery Act Transparency Statement|Sitemap|About US| Contact US: help@patsnap.com