Preparation method of polyaniline/attapulgite conductive composite material
A technology of conductive composite material and attapulgite, which is applied in the field of preparation of conductive materials to achieve high conductivity, simple synthesis process, and good stability of conductivity
- Summary
- Abstract
- Description
- Claims
- Application Information
AI Technical Summary
Problems solved by technology
Method used
Image
Examples
preparation example Construction
[0013] The present invention is the preparation method of polyaniline / attapulgite clay conductive composite material, and its steps are:
[0014] (1) Dissolve ionic liquid, attapulgite clay, aniline monomer, and dopant sulfamic acid in HCl solution with a concentration of 1mol / l, and stir vigorously for 0.5 hours at 0~40°C, the mass of ionic liquid The ratio of g to the mole of aniline monomer is: 1 to 10:0.011, the molar ratio of attapulgite mass g to the mole of aniline monomer is: 0.3 to 5:0.011, and the molar ratio of sulfamic acid to aniline monomer is: 0.9~5:1, the mass ratio of attapulgite to aqueous solution is 1:50~200;
[0015] (2) Slowly drop the oxidant ammonium persulfate solution into the above mixture, the solution turns dark green, react at 0~40°C for 30 minutes to 4 hours, the molar ratio of ammonium persulfate to aniline monomer is: 0.4~ 1.2:1;
[0016] (3) The mixed solution was sequentially suction-filtered and washed with distilled water until the filtra...
Embodiment 1
[0020] Dissolve 2.50g of ionic liquid, 0.03g of attapulgite, 0.0103mol of sulfamic acid, and 0.0110mol of aniline monomer into 50ml of 1mol / l hydrochloric acid solution, stir vigorously at normal temperature and pressure for 30min, and then add 10ml of persulfuric acid containing 0.066mol Ammonium hydrochloric acid solution (the concentration of hydrochloric acid is 1mol / l), stirred and reacted for 2 hours; the reaction solution was filtered and washed until the filtrate was neutral; finally, the filter cake was vacuum-dried at 40°C, and the dark green conductive material of the composite material was obtained after crushing. The conductivity of powder and tablet is 1.5 S·cm -1 .
Embodiment 2
[0022] Dissolve 5.00g of ionic liquid, 0.03g of attapulgite, 0.0103mol of sulfamic acid, and 0.0110mol of aniline monomer into 50ml of 1mol / l hydrochloric acid solution, stir vigorously at normal temperature and pressure for 30min, and then add 10ml of persulfuric acid containing 0.066mol Ammonium hydrochloric acid solution (the concentration of hydrochloric acid is 1mol / l), stirred and reacted for 2 hours; the reaction solution was filtered and washed until the filtrate was neutral; finally, the filter cake was vacuum-dried at 40°C, and the dark green conductive material of the composite material was obtained after crushing. The conductivity of powder and tablet is 10.0 S·cm -1 .
[0023] like figure 1 As shown, the attapulgite coated with polyaniline particles overlaps the gap between the polyaniline groups like a bridge. The diameter of the rod crystal in the attapulgite is on the order of 0.01 μm, and the length can reach 0.1-1 μm. figure 1 The diameter of the rod crysta...
PUM
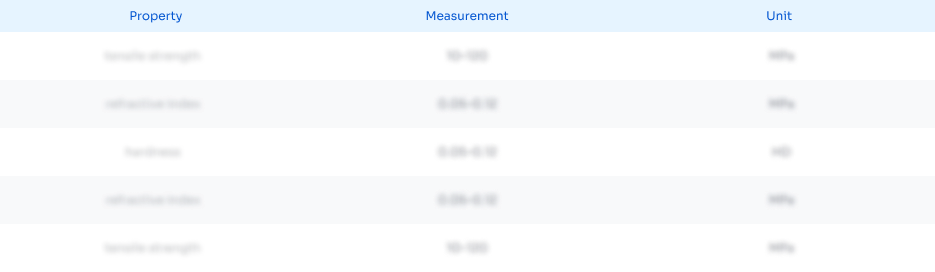
Abstract
Description
Claims
Application Information

- Generate Ideas
- Intellectual Property
- Life Sciences
- Materials
- Tech Scout
- Unparalleled Data Quality
- Higher Quality Content
- 60% Fewer Hallucinations
Browse by: Latest US Patents, China's latest patents, Technical Efficacy Thesaurus, Application Domain, Technology Topic, Popular Technical Reports.
© 2025 PatSnap. All rights reserved.Legal|Privacy policy|Modern Slavery Act Transparency Statement|Sitemap|About US| Contact US: help@patsnap.com