High-temperature resistant viscosity reducer for drilling fluids and preparation method for viscosity reducer
A high-temperature-resistant, viscosity-reducing agent technology, applied in the direction of chemical instruments and methods, drilling compositions, etc., can solve the problems of complex production process, difficulty in removing foam solids, high product cost, etc., and achieve simple preparation process and good viscosity reduction Effect, low-cost effect
- Summary
- Abstract
- Description
- Claims
- Application Information
AI Technical Summary
Problems solved by technology
Method used
Image
Examples
Embodiment 1
[0034] Add 80 parts of lignin, 100 parts of acrylic acid, 70 parts of maleic anhydride and 10 parts of iron powder into 510 parts of water, raise the temperature to 60-65 ° C for 2 hours; cool down to 50 ° C, add 55 parts of initiator; slowly add acrylonitrile 30 parts, react at 55-60°C for 2 hours; stop heating, add 35 parts of 30% ammonia water, 100 parts of potassium formate and 10 parts of iron powder, stir for 30 minutes and discharge to obtain high temperature anti-viscosity reducer for drilling fluid. Gained anti-high temperature viscosity reducer, investigate its performance, the results are shown in Table 1.
[0035] Table 1, embodiment 1 anti-high temperature viscosity reducer performance
[0036] project
Embodiment 2
[0038] Add 90 parts of lignin, 120 parts of acrylic acid, 50 parts of maleic anhydride and 20 parts of iron powder into 465 parts of water, raise the temperature to 60-75 ° C for 2 hours; cool down to 50 ° C, add 60 parts of initiator; slowly add acrylonitrile 40 parts, react at 50-70°C for 2 hours; stop heating, add 20 parts of sodium hydroxide, 120 parts of sodium formate and 15 parts of iron powder, stir for 30 minutes and discharge; that is, the anti-high temperature viscosity reducer for drilling fluid. The performance of the prepared anti-high temperature viscosity reducer was investigated, and the results are shown in Table 2.
[0039] Table 2, embodiment 2 anti-high temperature viscosity reducer performance
[0040] project
Embodiment 3
[0042] Add 50 parts of lignin, 80 parts of acrylic acid, 60 parts of maleic anhydride and 20 parts of iron powder into 475 parts of water, raise the temperature to 60-65 ° C for 2 hours; cool down to 50 ° C, add 55 parts of initiator; slowly add acrylonitrile 70 parts, react at 55-65°C for 2 hours; stop heating, add 25 parts of 30% ammonia water, 150 parts of sodium formate and 15 parts of iron powder, stir for 30 minutes and discharge to obtain high temperature anti-viscosity reducer for drilling fluid. The performance of the prepared anti-high temperature viscosity reducer was investigated, and the results are shown in Table 3.
[0043] Table 3, embodiment 3 anti-high temperature viscosity reducer performance
[0044] project
PUM
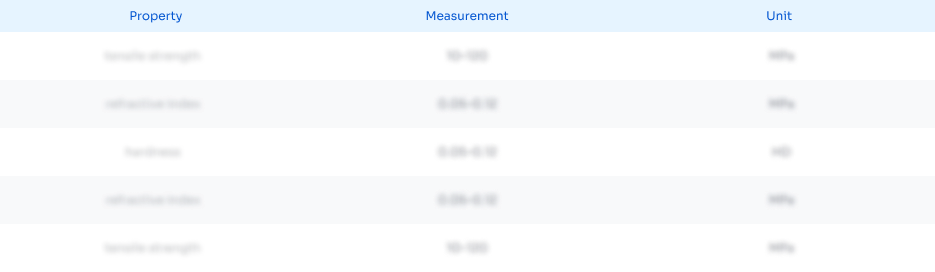
Abstract
Description
Claims
Application Information

- R&D
- Intellectual Property
- Life Sciences
- Materials
- Tech Scout
- Unparalleled Data Quality
- Higher Quality Content
- 60% Fewer Hallucinations
Browse by: Latest US Patents, China's latest patents, Technical Efficacy Thesaurus, Application Domain, Technology Topic, Popular Technical Reports.
© 2025 PatSnap. All rights reserved.Legal|Privacy policy|Modern Slavery Act Transparency Statement|Sitemap|About US| Contact US: help@patsnap.com