Production technology of silicon tetrafluoride
A silicon tetrafluoride and production process technology, applied in the direction of silicon halide compounds, halosilanes, etc., can solve the problems of high production cost of polysilicon, high production raw material cost, high energy consumption in the production process, and achieve less reaction materials and low raw material cost Low, the effect of small environmental pollution hazards
- Summary
- Abstract
- Description
- Claims
- Application Information
AI Technical Summary
Problems solved by technology
Method used
Examples
Embodiment 1
[0023] 1) Preheat the raw materials sodium fluorosilicate and silicon dioxide with a molar ratio of 1:0.1 to 100°C in a desiccator, dry and stir evenly;
[0024] 2) Transfer the dried sodium fluorosilicate and silica powder mixture into the reactor, spray into the H2O preheated to 70°C 2 SO4 content is the concentrated sulfuric acid of 98.0% to carry out stirring reaction, the H in the described sodium fluorosilicate and the concentrated sulfuric acid 2 The molar ratio of SO4 is 1:0.8, and the reactor is continuously heated during the reaction to keep the reaction temperature at 100°C;
[0025] 3) The gas generated during the reaction is extracted in time. The gas components are silicon tetrafluoride, hydrogen fluoride, water vapor and dust. After being washed with concentrated sulfuric acid to remove dust, absorb hydrogen fluoride, dehydrate, and remove acid mist, it enters the compressor for compression to obtain tetrafluoroethylene The molar concentration of the silicon di...
Embodiment 2
[0027] 1) Preheat the raw materials sodium fluorosilicate and silicon dioxide with a molar ratio of 1:0.5 to 70°C in a desiccator, dry and stir evenly;
[0028] 2) Transfer the dried sodium fluorosilicate and silica powder mixture into the reactor, spray into the H2O preheated to 100°C 2 The concentrated sulfuric acid of SO4 content 99.0% carries out stirring reaction, and the H in the described sodium fluorosilicate and the concentrated sulfuric acid 2 The molar ratio of SO4 is 1:1.1, and the reactor is continuously heated during the reaction to keep the reaction temperature at 150°C;
[0029] 3) The gas generated during the reaction is extracted in time. The gas components are silicon tetrafluoride, hydrogen fluoride, water vapor and dust. After being washed with concentrated sulfuric acid to remove dust, absorb hydrogen fluoride, dehydrate, and remove acid mist, it enters the compressor for compression to obtain tetrafluoroethylene Siliconization product, the solid reactio...
Embodiment 3
[0031] 1) Preheat the raw materials sodium fluorosilicate and silicon dioxide with a molar ratio of 1:1.0 to 180°C in a desiccator, dry and stir evenly;
[0032] 2) Transfer the dried sodium fluorosilicate and silica powder mixture into the reactor, spray into the H2O preheated to 120°C 2 The concentrated sulfuric acid of SO4 content 98.0% carries out stirring reaction, and the H in the described sodium fluorosilicate and the concentrated sulfuric acid 2 The molar ratio of SO4 is 1:1.3, and the reactor is continuously heated during the reaction to keep the reaction temperature at 200°C;
[0033] 3) The gas generated during the reaction is extracted in time. The gas components are silicon tetrafluoride, hydrogen fluoride, water vapor and dust. After being washed with concentrated sulfuric acid to remove dust, absorb hydrogen fluoride, dehydrate, and remove acid mist, it enters the compressor for compression to obtain tetrafluoroethylene The molar content of the silicon dioxide...
PUM
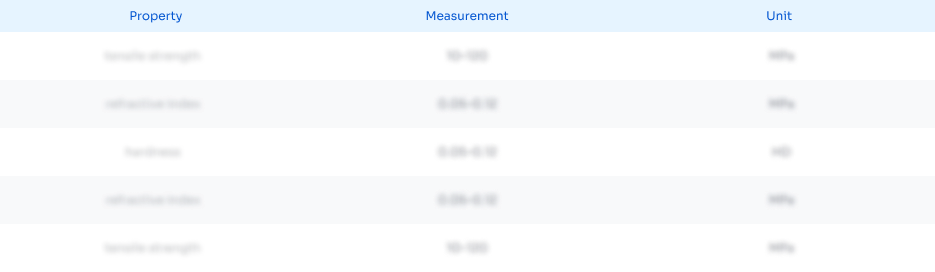
Abstract
Description
Claims
Application Information

- Generate Ideas
- Intellectual Property
- Life Sciences
- Materials
- Tech Scout
- Unparalleled Data Quality
- Higher Quality Content
- 60% Fewer Hallucinations
Browse by: Latest US Patents, China's latest patents, Technical Efficacy Thesaurus, Application Domain, Technology Topic, Popular Technical Reports.
© 2025 PatSnap. All rights reserved.Legal|Privacy policy|Modern Slavery Act Transparency Statement|Sitemap|About US| Contact US: help@patsnap.com