Gravity separation and floatation combined separating technology for antimony oxide ores
An antimony oxide and process technology, which is applied in the field of antimony oxide ore re-floating combined separation process, can solve the problems of low ore grade, waste of heat, non-compliance with energy saving and emission reduction, etc., and achieve the effect of improving grade and recovery rate.
- Summary
- Abstract
- Description
- Claims
- Application Information
AI Technical Summary
Problems solved by technology
Method used
Examples
Embodiment 1
[0015] The antimony oxide raw ore containing 1.52% Sb is ground, and the particle size of the grinding product is -0.074mm, which accounts for 80%. 25-30%, use NaOH to adjust the pH of the pulp to 9-10, add 50g / t of decanyl primary amine, reverse flotation to obtain carbonate and a small amount of silicate gangue mineral tailings, and use H 2 SO 4 Adjust the pH to 6-7, add lead chloride 30g / t, add humic acid (sodium) 40g / t, add dodecyl sulfate 60g / t to flotation to obtain antimony oxide concentrate, and the product in the tank is silicate Gangue mineral tailings, shaker tailings and flotation tailings are combined into total tailings. The test indicators are shown in Table 1.
[0016] Table 1 Antimony oxide ore separation index 1
[0017] product name
Embodiment 2
[0019] Grind the antimony oxide raw ore containing 3.14% Sb. The particle size of the grinding product is -0.074mm, accounting for 75%. 25-30%, use NaOH to adjust the pH of the pulp to 10-11, add 60g / t of dodecyl primary amine, reverse flotation to obtain carbonate and a small amount of silicate gangue mineral tailings, and use H 2 SO 4 Adjust the pH to 6-7, add copper sulfate 50g / t, add humic acid (sodium) 45g / t, add cetyl sulfate 75g / t to get antimony oxide concentrate, and the product in the tank is silicate veins Rock mineral tailings, shaker tailings and flotation tailings are combined into total tailings, and the test indicators are shown in Table 2.
[0020] Table 2 Separation index 2 of antimony oxide ore
[0021] product name
Embodiment 3
[0023] The raw ore containing 7.53% Sb antimony oxide is ground, the particle size of the grinding product is -0.074mm, accounting for 70%, and it is pre-enriched through the spiral chute. -30%, use NaOH to adjust the pH of the pulp to 10-11, add octadecyl primary amine 60g / t, reverse flotation to obtain carbonate and a small amount of silicate gangue mineral tailings, the product in the tank is washed with H 2 SO 4 Adjust the pH to 6.5-7.5, add copper sulfate 50g / t, add humic acid (sodium) 30g / t, add cetyl sulfate 85g / t to obtain antimony oxide concentrate, and the product in the tank is silicate veins Rock mineral tailings, the tailings of the spiral chute and the flotation tailings are combined into the total tailings, and the test indicators are shown in Table 3.
[0024] Table 3 Antimony Ore Separation Index 3
[0025] product name
[0026] The test results from Tables 1 to 3 show that using the antimony oxide ore refloating combined separation process of the...
PUM
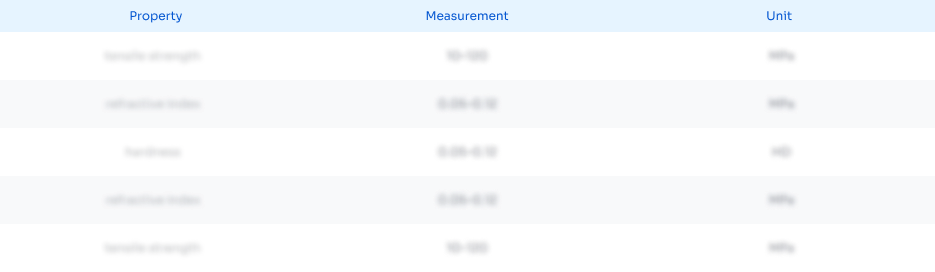
Abstract
Description
Claims
Application Information

- R&D
- Intellectual Property
- Life Sciences
- Materials
- Tech Scout
- Unparalleled Data Quality
- Higher Quality Content
- 60% Fewer Hallucinations
Browse by: Latest US Patents, China's latest patents, Technical Efficacy Thesaurus, Application Domain, Technology Topic, Popular Technical Reports.
© 2025 PatSnap. All rights reserved.Legal|Privacy policy|Modern Slavery Act Transparency Statement|Sitemap|About US| Contact US: help@patsnap.com