Normal-temperature phosphating solution and method for preparing same
A phosphating solution and normal temperature technology, which is applied in the coating process of metal materials, etc., can solve problems such as difficulty in stabilizing the concentration of hydrogen peroxide in the phosphating solution, affecting the quality of processed products, and easily generating phosphating residues, etc., so as to improve the phosphating effect , Saving phosphating process, highlighting the effect of substantive features
- Summary
- Abstract
- Description
- Claims
- Application Information
AI Technical Summary
Problems solved by technology
Method used
Examples
Embodiment 1
[0024] Hydroxylammonium sulfate 0.5% Phosphoric acid 18% Sodium dihydrogen phosphate 2%
[0025] Fatty alcohol polyoxyethylene ether 0.5% cerium nitrate 0.6% zinc oxide 4%
[0026] Manganese phosphate 2%, the balance is water.
[0027] Take zinc oxide and add a small amount of water to make a paste, slowly add phosphoric acid to it, keep stirring until it becomes a transparent and clear liquid, and mix well; then add manganese phosphate, cerium nitrate, sodium dihydrogen phosphate, hydroxylammonium sulfate and fatty alcohol in sequence Polyoxyethylene ether, stir while adding, mix well, add the remaining amount of water, mix well, and stand for 2 hours to get it.
Embodiment 2
[0029] Hydroxylammonium sulfate 0.1% Phosphoric acid 24% Sodium dihydrogen phosphate 5%
[0030] Fatty alcohol polyoxyethylene ether 2% cerium nitrate 1% zinc oxide 8%
[0031] Manganese phosphate 4%, the balance is water.
[0032] Take zinc oxide and add a small amount of water to make a paste, slowly add phosphoric acid to it, keep stirring until it becomes a transparent and clear liquid, and mix well; then add manganese phosphate, cerium nitrate, sodium dihydrogen phosphate, hydroxylammonium sulfate and fatty alcohol in sequence Polyoxyethylene ether, stir while adding, mix uniformly, add the remaining amount of water, mix uniformly, and leave it for 6 hours to get it.
Embodiment 3
[0034] Hydroxylammonium sulfate 0.6 Phosphoric acid 22% Sodium dihydrogen phosphate 4%
[0035] Fatty alcohol polyoxyethylene ether 1% cerium nitrate 0.8% zinc oxide 6%
[0036] 3% of manganese phosphate, the balance is water.
[0037] Take zinc oxide and add a small amount of water to make a paste, slowly add phosphoric acid to it, keep stirring until it becomes a transparent and clear liquid, and mix well; then add manganese phosphate, cerium nitrate, sodium dihydrogen phosphate, hydroxylammonium sulfate and fatty alcohol in sequence Polyoxyethylene ether, stir while adding, mix uniformly, add the remaining amount of water, mix uniformly, and stand for 4 hours to get it.
PUM
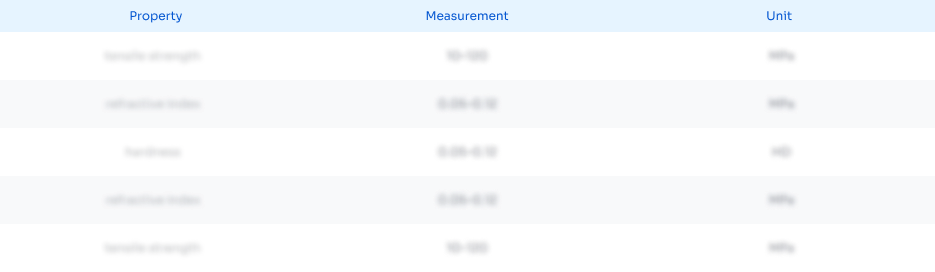
Abstract
Description
Claims
Application Information

- R&D Engineer
- R&D Manager
- IP Professional
- Industry Leading Data Capabilities
- Powerful AI technology
- Patent DNA Extraction
Browse by: Latest US Patents, China's latest patents, Technical Efficacy Thesaurus, Application Domain, Technology Topic, Popular Technical Reports.
© 2024 PatSnap. All rights reserved.Legal|Privacy policy|Modern Slavery Act Transparency Statement|Sitemap|About US| Contact US: help@patsnap.com