Preparation method for natural plant fiber plastic
A natural plant fiber and plastic technology, which is applied in the field of preparation of natural plant fiber plastic, can solve the problems of poor performance, difficulty and poor compatibility of cellulose
- Summary
- Abstract
- Description
- Claims
- Application Information
AI Technical Summary
Problems solved by technology
Method used
Examples
Embodiment Construction
[0012] A preparation method of natural plant fiber plastic, comprising 59.5%-69.5% matrix resin, 30%-40% hemp fiber, 0.1%-0.4% compatibilizer, 0.1%-0.4% anti-aging additive, in order to obtain corresponding different Strong material, the first step is to melt 59.5%-69.5% matrix resin, 0.1%-0.4% compatibilizer, 0.1%-0.4% anti-aging additives to obtain molten resin; the second step is to melt the resin in the molten resin Add 30%-40% hydrophobically modified hemp fiber without free water for blending; the third step, after blending, when the hemp fiber is uniformly dispersed in the matrix resin, it is extruded and granulated by a short screw, and finally granulated Processing, the finely ground granules are dried and then added with an adhesive to make granules with a particle size of about 0.1 mm. The specific proportions, the proportion of matrix resin is 59.5%, the proportion of hemp fiber is 40%, the proportion of compatibilizer is 0.4%, and the proportion of anti-aging addi...
PUM
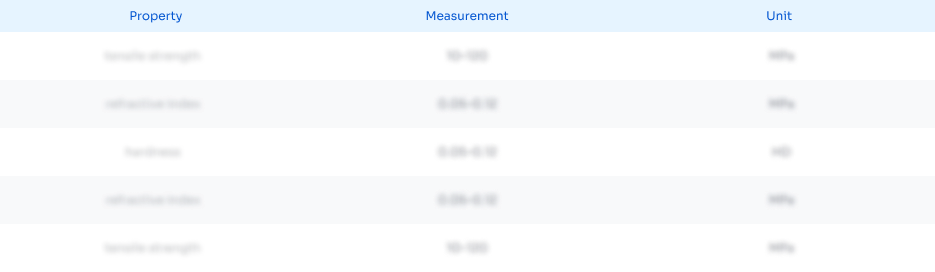
Abstract
Description
Claims
Application Information

- R&D Engineer
- R&D Manager
- IP Professional
- Industry Leading Data Capabilities
- Powerful AI technology
- Patent DNA Extraction
Browse by: Latest US Patents, China's latest patents, Technical Efficacy Thesaurus, Application Domain, Technology Topic, Popular Technical Reports.
© 2024 PatSnap. All rights reserved.Legal|Privacy policy|Modern Slavery Act Transparency Statement|Sitemap|About US| Contact US: help@patsnap.com