Manufacturing method of high-calcium solid sulfur ash aerated concrete building blocks
A high-calcium sulfur-fixing ash and aerated concrete technology, applied in the field of building materials, can solve the problems of low compressive strength and post-freezing strength, difficult process control, and easy plugging of pipes, etc., to achieve compressive strength and freezing The effect of high final strength, simple process flow, and not easy to crack and deform
- Summary
- Abstract
- Description
- Claims
- Application Information
AI Technical Summary
Problems solved by technology
Method used
Image
Examples
Embodiment 1
[0013] Embodiment 1 of the present invention: calculated by weight, get 50 parts of high-calcium sulfur-fixing ash, 20 parts of fly ash, 9 parts of ordinary Portland cement whose label is 42.5, and the siliceous material of finely ground silica sand or microsilica fume 5 parts of lime, 15 parts of lime, 1 part of gypsum, and 0.06 parts of aluminum powder are used as raw materials. The sulfur trioxide content of the high-calcium sulfur-fixing ash should be controlled within the range of 4.5% to 15%, and the free calcium oxide content should be controlled within 1.8%. ~10% range; gypsum can be natural gypsum or phosphogypsum or desulfurized gypsum from industrial by-products; lime should be ground quicklime, and the sum of the percentages of CaO and MgO in the ground quicklime should be controlled at CaO+MgO ≥75% range; then put high-calcium sulfur-fixing ash, fly ash, siliceous materials and gypsum together into a ball mill for mixing and ball milling for 5 to 20 minutes, then...
Embodiment 2
[0014] Embodiment 2 of the present invention: calculated by weight, get 70 parts of high-calcium sulfur-fixing ash, 30 parts of fly ash, 10 parts of ordinary Portland cement whose label is 42.5, and the siliceous material of finely ground silica sand or microsilica fume 10 parts of lime, 16 parts of lime, 1 part of gypsum, and 0.06 parts of aluminum powder are used as raw materials. The sulfur trioxide content of the high-calcium sulfur-fixing ash should be controlled within the range of 4.5% to 15%, and the free calcium oxide content should be controlled within 1.8%. ~10% range; gypsum can be natural gypsum or phosphogypsum or desulfurized gypsum from industrial by-products; lime should be ground quicklime, and the sum of the percentages of CaO and MgO in the ground quicklime should be controlled at CaO+MgO ≥75% range; then put high-calcium sulfur-fixed ash, fly ash, siliceous materials, and gypsum into the mixer and add water to stir it. The weight of water added is 0.3 to ...
PUM
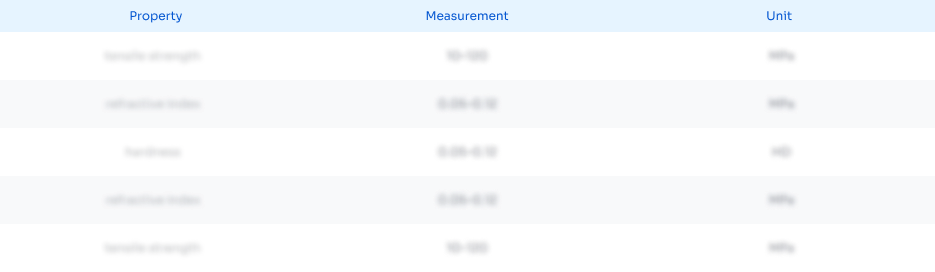
Abstract
Description
Claims
Application Information

- R&D
- Intellectual Property
- Life Sciences
- Materials
- Tech Scout
- Unparalleled Data Quality
- Higher Quality Content
- 60% Fewer Hallucinations
Browse by: Latest US Patents, China's latest patents, Technical Efficacy Thesaurus, Application Domain, Technology Topic, Popular Technical Reports.
© 2025 PatSnap. All rights reserved.Legal|Privacy policy|Modern Slavery Act Transparency Statement|Sitemap|About US| Contact US: help@patsnap.com