Method for treating claus technical tail gas
A technology of process tail gas and oxygen, applied in the direction of separation methods, chemical instruments and methods, inorganic chemistry, etc., can solve the problems of equipment investment, operation cost, energy consumption, air pollution, and less promotion and application, so as to reduce the burden on the atmospheric environment, The effect of low cost and simple process
- Summary
- Abstract
- Description
- Claims
- Application Information
AI Technical Summary
Problems solved by technology
Method used
Image
Examples
Embodiment 1
[0029] A natural gas chemical plant Claus process tail gas, SO in the gas 2 The content is 4235ppm, O 2 The content is 3vol%, and the water vapor content is 22vol%, from which a part of the process tail gas is drawn for testing. 30mL of columnar activated coke and 10mL of activated carbon fiber (catalyst) were placed in a fixed bed reactor with an inner diameter of 22mm and a length of 200mm. Raise the temperature to 60°C and ventilate the reaction. Gas flow rate 400mL / min, space velocity 600h -1 . While the tail gas continuously passes through the catalyst bed, water as a regenerated washing agent is also continuously passed into the catalyst bed from above, and the flow rate is 0.1-0.8 times the volume flow rate of the treated gas. In this embodiment, the flow rate of water is 50mL / min. After the sulfur dioxide in the exhaust gas is removed by oxidation reaction, the regenerated detergent becomes dilute sulfuric acid. Experimental results: The steady-state desulfurizat...
Embodiment 2
[0031] The gas composition is the same as in Example 1. A part of the process tail gas is extracted from it and continuously enters the fixed-bed reactor filled with 40mL spherical activated carbon desulfurizer from the lower inlet. The inner diameter of the reactor is 22mm and the length is 200mm. Strictly control the working temperature of the bed at 80°C, the gas flow at 533mL / min, and the space velocity at 800h -1 . While the tail gas continuously passes through the catalyst bed, dilute sulfuric acid is collected at the outlet of the reactor. The collected dilute sulfuric acid (initial acid concentration is 5%) is continuously returned to the catalyst bed from above as a regenerated detergent, and the tail gas is desulfurized by activated carbon. The surface of the agent reaches a dynamic equilibrium of adsorption-catalytic oxidation-desorption. Experimental results: The steady-state desulfurization rate is 89%, and the acid concentration reaches 40%.
[0032] Because t...
Embodiment 3
[0034] The gas composition is the same as in Example 1. 30 mL of columnar activated coke and 10 mL of activated carbon fiber are placed in a fixed-bed reactor, and the volume of the reactor is the same as in Example 1. Raise the temperature to 120°C and ventilate the reaction. Gas flow rate 3333mL / min, space velocity 5000h -1 . While the tail gas continuously passes through the catalyst bed, the water vapor as the regenerated detergent is also continuously passed into the catalyst bed from above. After the sulfur dioxide in the exhaust gas is removed by oxidation reaction, the regenerated detergent becomes dilute sulfuric acid. Dilute sulfuric acid is re-introduced into the catalyst bed. Experimental results: The steady-state desulfurization rate is 81%, and the final acid concentration reaches 25%.
PUM
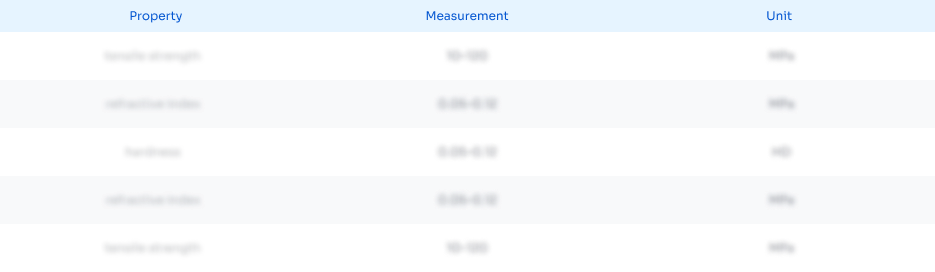
Abstract
Description
Claims
Application Information

- R&D
- Intellectual Property
- Life Sciences
- Materials
- Tech Scout
- Unparalleled Data Quality
- Higher Quality Content
- 60% Fewer Hallucinations
Browse by: Latest US Patents, China's latest patents, Technical Efficacy Thesaurus, Application Domain, Technology Topic, Popular Technical Reports.
© 2025 PatSnap. All rights reserved.Legal|Privacy policy|Modern Slavery Act Transparency Statement|Sitemap|About US| Contact US: help@patsnap.com