Preparation method for hydrorefining catalyst
A hydrogenation catalyst and hydrorefining technology, applied in chemical instruments and methods, metal/metal oxide/metal hydroxide catalysts, physical/chemical process catalysts, etc., can solve the problem of reducing the dispersion of metal active components, carrier The problems of limited pore surface area and limited catalyst activity can achieve the effect of multiple hydrogenation reaction active sites, uniform distribution of metal components, and simple method.
- Summary
- Abstract
- Description
- Claims
- Application Information
AI Technical Summary
Problems solved by technology
Method used
Image
Examples
Embodiment 1
[0020] This example illustrates the preparation method of the catalyst of the present invention.
[0021] Weigh 500g of aluminum hydroxide dry glue, 68g of basic nickel carbonate, and 20g of polyethylene glycol. After fully mixing the three dry powder materials with a pulverizer, add 2wt% nitric acid solution and knead them, and extrude them with an extruder. , the extrudate was dried at 120°C for 20 hours and calcined at 400°C for 5 hours to obtain NiO-Al 2 o 3 Complex. Weigh 15.9g of ammonium molybdate heptahydrate and dissolve it in 300g of deionized water, add 1.8g of urea and 30g of ethylene glycol, stir the mixed solution well and pour it into the autoclave, weigh 17g of the prepared nickel oxide-alumina composite Put it into the autoclave, close the reaction kettle, heat up to 100°C for 20 hours; cool to room temperature, open the reaction kettle, take out the catalyst, filter, wash with water, dry the obtained product in an oven at 120°C for 10 hours, and roast at 500°...
Embodiment 2
[0023] This example illustrates the preparation method of the catalyst of the present invention.
[0024] Weigh 500g of aluminum hydroxide dry glue, 68g of basic nickel carbonate, and 20g of polyethylene glycol. After fully mixing the three dry powder materials with a pulverizer, add 2wt% nitric acid solution and knead them, and extrude them with an extruder. , The extruded product was dried at 120°C for 20 hours and calcined at 400°C for 5 hours to obtain a nickel oxide-alumina composite. Weigh 15.9g of ammonium molybdate heptahydrate and dissolve it in 300g of deionized water, add 1.8g of urea and 30g of ethylene glycol, stir the mixed solution well and pour it into the autoclave, weigh 17g of the prepared nickel oxide-alumina composite Put it into an autoclave, close the reaction kettle, heat up to 150°C and react for 20 hours; cool to room temperature, open the reaction kettle, take out the catalyst, filter, wash with water, dry the obtained product in an oven at 120°C for...
Embodiment 3
[0026] This example illustrates the preparation method of the catalyst of the present invention.
[0027] Weigh 500g of aluminum hydroxide dry glue, 85g of basic nickel carbonate, and 20g of polyethylene glycol, fully mix the three kinds of dry powder materials with a pulverizer, add 2wt% nitric acid solution and knead, and extrude them with an extruder , The extruded product was dried at 120°C for 20 hours and calcined at 400°C for 5 hours to obtain a nickel oxide-alumina composite. Weigh 15.9g of ammonium molybdate heptahydrate and dissolve it in 300g of deionized water, add 1.8g of urea and 30g of ethylene glycol, stir the mixed solution well and pour it into the autoclave, weigh 17g of the prepared nickel oxide-alumina composite Put it into an autoclave, close the reaction kettle, heat up to 150°C and react for 20 hours; cool to room temperature, open the reaction kettle, take out the catalyst, filter, wash with water, dry the obtained product in an oven at 120°C for 10 ho...
PUM
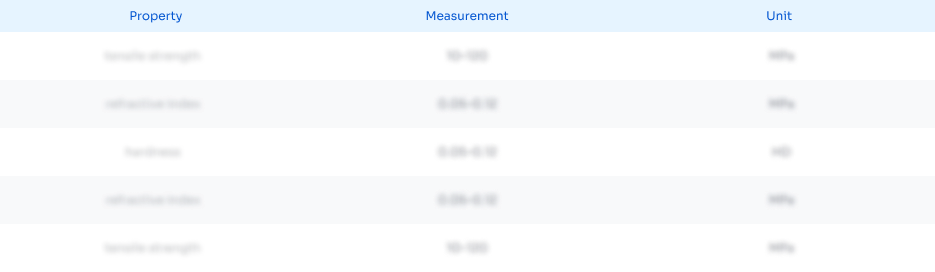
Abstract
Description
Claims
Application Information

- Generate Ideas
- Intellectual Property
- Life Sciences
- Materials
- Tech Scout
- Unparalleled Data Quality
- Higher Quality Content
- 60% Fewer Hallucinations
Browse by: Latest US Patents, China's latest patents, Technical Efficacy Thesaurus, Application Domain, Technology Topic, Popular Technical Reports.
© 2025 PatSnap. All rights reserved.Legal|Privacy policy|Modern Slavery Act Transparency Statement|Sitemap|About US| Contact US: help@patsnap.com