Method for extracting silver from silver-containing crude tin alloy
A technology of tin alloy and crude tin, which is applied in the field of extracting silver from crude tin by pyrometallurgy technology, can solve the problems of high investment cost, poor working conditions, and low direct tin recovery rate of electrolysis, and achieve huge environmental protection benefits and economic benefits. Benefits, safe and controllable process, and high recovery rate
- Summary
- Abstract
- Description
- Claims
- Application Information
AI Technical Summary
Problems solved by technology
Method used
Image
Examples
Embodiment 1
[0018] (1) Heat up 10t of silver-containing coarse tin alloy with a silver content of 40g / t (the balance is Sn) to 430°C in a silver pot for melting;
[0019] (2) adding zinc ingots to the melted silver-containing crude tin alloy obtained in step (1), and stirring to dissolve;
[0020] (3) Lower the temperature of the dissolved mixture in step (2) to 390°C, insert the drum of the submersible centrifuge into the silver extraction pot, and rotate the rotating shaft at 300 rpm for 10-15 minutes for centrifugation. At this time, the silver The zinc slag enters the drum, lifts the drum to the liquid surface, and centrifuges at a speed of 400 rpm. The tin liquid is thrown out tangentially along the sieve hole of the drum, and the silver-zinc slag stays in the drum. Then insert the drum into the silver extraction pot, and then carry out the next cycle of operation until there is no scum on the surface of the upper liquid, that is, the upper layer is tin liquid, and the lower layer is...
Embodiment 2
[0023] (1) Heat 10t of silver-containing coarse tin alloy (the balance is Sn) with a silver content of 10000g / t to 460°C for melting;
[0024] (2) adding zinc ingots to the melted silver-containing crude tin alloy obtained in step (1), and stirring to dissolve;
[0025] (3) Cool down the dissolved mixture in step (2) to 395°C, and then perform centrifugation at a speed of 200 rpm until there is no scum on the surface of the upper liquid, that is, the upper layer is tin liquid, and the lower layer is silver-zinc slag; the obtained tin liquid is naturally cooled and solidified into a tin alloy after removing silver;
[0026] (4) The silver and zinc slag obtained in step (3) is vacuum distilled to obtain silver and crude zinc. The silver content in the tin alloy after silver extraction is 6g / t.
Embodiment 3
[0028] (1) Heat 10t of silver-containing coarse tin alloy (the balance is Sn) with a silver content of 50,000g / t to 500°C for melting;
[0029] (2) adding zinc ingots to the melted silver-containing crude tin alloy obtained in step (1), and stirring to dissolve;
[0030] (3) Cool down the dissolved mixture in step (2) to 400°C, and then perform centrifugation at a speed of 700 rpm until there is no scum on the surface of the upper liquid, that is, the upper layer is tin liquid, and the lower layer is silver-zinc slag; the obtained tin liquid is naturally cooled and solidified into a tin alloy after removing silver;
[0031] (4) The silver-zinc slag obtained in step (3) is vacuum distilled to obtain silver and crude zinc, and the obtained crude zinc is returned to step (2) for recycling. The silver content in the tin alloy after silver extraction is 8g / t.
PUM
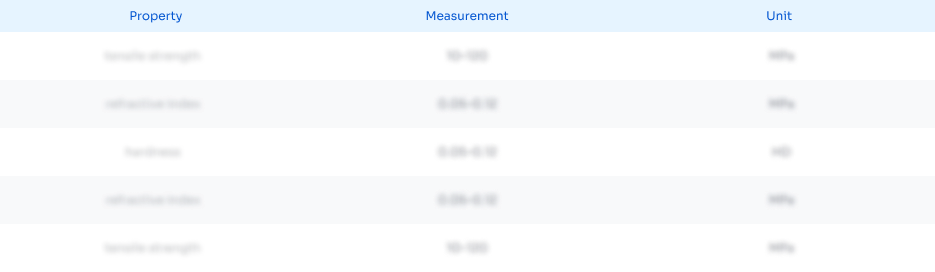
Abstract
Description
Claims
Application Information

- R&D
- Intellectual Property
- Life Sciences
- Materials
- Tech Scout
- Unparalleled Data Quality
- Higher Quality Content
- 60% Fewer Hallucinations
Browse by: Latest US Patents, China's latest patents, Technical Efficacy Thesaurus, Application Domain, Technology Topic, Popular Technical Reports.
© 2025 PatSnap. All rights reserved.Legal|Privacy policy|Modern Slavery Act Transparency Statement|Sitemap|About US| Contact US: help@patsnap.com