Catalyst and method used for preparing 1,3-butadiene by oxidative dehydrogenation of n-butene
A technology for oxidative dehydrogenation and catalysts, applied in chemical instruments and methods, physical/chemical process catalysts, metal/metal oxides/metal hydroxide catalysts, etc., can solve the problem of poor catalytic activity and selectivity, and the inability to obtain effective C4 fractions Utilization and other issues to achieve high activity, selectivity, and efficient utilization
- Summary
- Abstract
- Description
- Claims
- Application Information
AI Technical Summary
Problems solved by technology
Method used
Image
Examples
Embodiment 1
[0030] Catalyst preparation process
[0031] In a 500mL beaker, add 21.78gFe(NO 3 ) 3 9H 2 O, 8.02gZn(NO 3 ) 2 ·6H 2 O, 1.17gCo(NO 3 ) 3 ·6H 2 O, 0.21gMg(NO 3 ) 2 ·6H 2 O and 200mL deionized water, wherein the molar ratio of iron to zinc is 2:1, the molar ratio of cobalt to zinc is 0.15:1, and the molar ratio of magnesium to zinc is 0.03:1, stir to dissolve it, and add the mass fraction It is 25% ammonia solution, adjust the pH value of the solution to 9, after the dropwise addition, heat to 60°C and stir for 1h, cool to 20°C, filter with a Buchner funnel, wash the filter cake with deionized water until neutral, the obtained solid is in After drying at 120°C for 10 hours, place it in a muffle furnace and bake at 600°C for 8 hours, cool, grind, and sieve to obtain a 20-60 mesh cobalt and magnesium-modified zinc ferrite catalyst, which is sealed and stored.
[0032] Oxidative Dehydrogenation Process
[0033] Fill 2mL of the above catalyst into a stainless steel reac...
Embodiment 2
[0036] Catalyst preparation process
[0037] In a 500mL beaker, add 21.78gFe(NO 3 ) 3 9H 2 O, 8.02gZn(NO 3 ) 2 ·6H 2 O, 0.39gCo(NO 3 ) 3 ·6H 2 O, 0.21gMg(NO 3 ) 2 ·6H 2 O and 200mL deionized water, wherein the molar ratio of iron to zinc is 2:1, the molar ratio of cobalt to zinc is 0.05:1, and the molar ratio of magnesium to zinc is 0.03:1, stir to dissolve it, and add the mass fraction It is 25% ammonia solution, adjust the pH value of the solution to 10, after the dropwise addition, heat to 50°C and stir for 2h, cool to 20°C, filter with Buchner funnel, wash the filter cake with deionized water until neutral, the obtained solid is in After drying at 100°C for 12 hours, place it in a muffle furnace and bake at 500°C for 10 hours, cool, grind, and sieve to obtain a 20-60 mesh cobalt and magnesium-modified zinc ferrite catalyst, which is sealed and stored.
[0038] Oxidative Dehydrogenation Process
[0039] Fill 2mL of the above catalyst into a stainless steel reac...
Embodiment 3
[0042] Catalyst preparation process
[0043] In a 500mL beaker, add 21.78gFe(NO 3 ) 3 9H 2 O, 8.02gZn(NO 3 ) 2 ·6H 2 O, 1.17gCo(NO 3 ) 3 ·6H 2 O, 0.07gMg(NO 3 ) 2 ·6H 2 O and 200mL deionized water, wherein the molar ratio of iron to zinc is 2:1, the molar ratio of cobalt to zinc is 0.15:1, and the molar ratio of magnesium to zinc is 0.01:1, stir to dissolve it, and add the mass fraction It is 25% ammonia solution, adjust the pH value of the solution to 9, after the dropwise addition, heat to 70°C and stir for 0.5h, cool to 20°C, filter with a Buchner funnel, wash the filter cake with deionized water until neutral, the obtained solid After drying at 140°C for 8 hours, place it in a muffle furnace and bake at 700°C for 6 hours, cool, grind, and sieve to obtain a 20-60 mesh cobalt and magnesium-modified zinc ferrite catalyst, which is sealed and stored.
[0044] Oxidative Dehydrogenation Process
[0045] Fill 2mL of the above catalyst into a stainless steel reactor w...
PUM
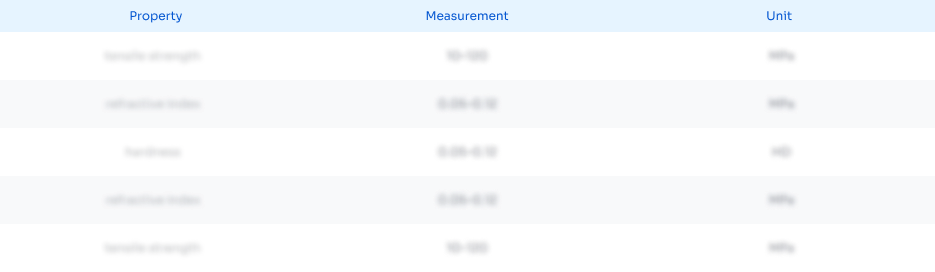
Abstract
Description
Claims
Application Information

- R&D
- Intellectual Property
- Life Sciences
- Materials
- Tech Scout
- Unparalleled Data Quality
- Higher Quality Content
- 60% Fewer Hallucinations
Browse by: Latest US Patents, China's latest patents, Technical Efficacy Thesaurus, Application Domain, Technology Topic, Popular Technical Reports.
© 2025 PatSnap. All rights reserved.Legal|Privacy policy|Modern Slavery Act Transparency Statement|Sitemap|About US| Contact US: help@patsnap.com