Method, device, program, and computer readable recording medium for failure analysis of spot welded section
一种分析方法、点焊的技术,应用在分析材料、测量装置、焊接设备等方向,能够解决花费制作成本、未达到稳定纵弯曲形态、断裂等问题,达到研究容易的效果
- Summary
- Abstract
- Description
- Claims
- Application Information
AI Technical Summary
Problems solved by technology
Method used
Image
Examples
Embodiment 1
[0118] In Table 3, the experimental conditions and experimental results of Example 1 are shown.
[0119] [table 3]
[0120]
[0121] exist Figure 8 And Table 4 shows the analysis conditions and analysis results of Example 1. In Invention Examples 1 to 7, the fracture mode is load-type fracture, and the error of the fracture load is -2.6%, which is relatively small. In Table 3, the load-type fracture occurred in the experiment, so it is ideal to use the load-type fracture method for analysis as in Invention Examples 1 to 7, but in analysis, the deformation is advancing and the force or moment applied to the welded part is in the Therefore, fracture prediction can be performed in a method other than the load-based fracture method. Inventive examples 8 to 10 are the fracture judgment results of the torque type fracture mode, and inventive examples 11 to 13 are the fracture judgment results of the internal solder joint fracture mode. As shown in Table 4, the accuracy of th...
Embodiment 2
[0125] In Table 5, the experimental conditions and experimental results of Example 2 are shown. In Inventive Example 1 and Comparative Example 2, the fracture mode was load fracture.
[0126] [table 5]
[0127]
[0128] When it is Invention Example 1, such as Figure 9A , Figure 9B As shown, the fractured part of the spot weld and the deformed shape of the test body are in good agreement with the experiment. On the other hand, in Comparative Example 2, the allowable load value at each moment after reaching the maximum allowable load value of the welded portion is not obtained, and the allowable load value becomes 0 immediately after reaching the maximum allowable load value. In this case, it was found that the interlocking spot welds fractured and fractures occurred in all the spot welds of the hat test body, which was inconsistent with the experimental results.
Embodiment 3
[0130] The experimental conditions of Example 3 are shown in Table 6.
[0131] [Table 6]
[0132]
[0133] The main dimensions of the test bodies used in Example 3 are shown below.
[0134] Cap: The straight line at the bottom of the cap is 45mm, the width of the flange is 20mm, the height of the section is 43mm, and the overall length is 370mm
[0135] Flat plate: width 100mm, length 360mm
[0136] Spot welding interval: 40mm
[0137] The test conditions of Example 3 are shown below.
[0138] Drop hammer shaft crush test: drop hammer weight 140kg, initial velocity 36km / h
[0139] In either example, the effective width was 20 mm of the flange width to the cap side member, and 50 mm, which is half the width, to the flat plate. As a result of the test, plug welding fractures occurred at two points.
[0140] exist Figure 10 And Table 7 shows the analysis conditions and analysis results of Example 3. As shown in Example 1, in the test in which the cross-sectional shape ...
PUM
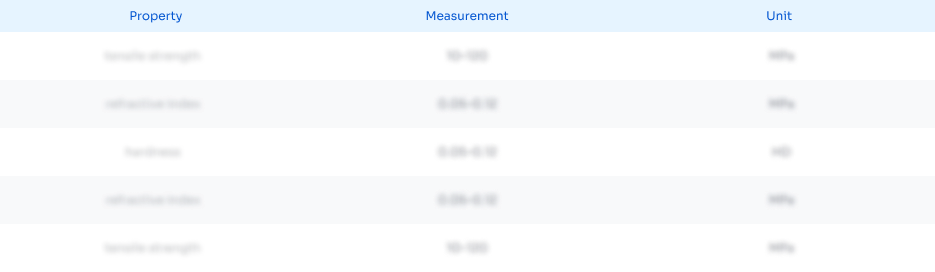
Abstract
Description
Claims
Application Information

- R&D
- Intellectual Property
- Life Sciences
- Materials
- Tech Scout
- Unparalleled Data Quality
- Higher Quality Content
- 60% Fewer Hallucinations
Browse by: Latest US Patents, China's latest patents, Technical Efficacy Thesaurus, Application Domain, Technology Topic, Popular Technical Reports.
© 2025 PatSnap. All rights reserved.Legal|Privacy policy|Modern Slavery Act Transparency Statement|Sitemap|About US| Contact US: help@patsnap.com